Categories: Novice electricians, Electric motors and their application
Number of views: 41987
Comments on the article: 4
Mechanical and electrical characteristics of induction motors
This article will highlight the topic of mechanical and electrical characteristics of electric motors. Using an asynchronous motor as an example, consider such parameters as power, work, efficiency, cosine phi, torque, angular velocity, linear speed and frequency. All these characteristics are important when designing equipment in which electric motors serve as drive motors. Especially asynchronous electric motors are especially widespread in the industry today, so we will dwell on their characteristics. For example, consider the AIR80V2U3.
Rated mechanical power of an induction motor
The nameplate (on the nameplate) of the motor always indicates the rated mechanical power on the shaft of the motor. This is not the electric power that this electric motor consumes from the network.
So, for example, for an AIR80V2U3 engine, a rating of 2200 watts corresponds precisely to the mechanical power on the shaft. That is, in optimal operating mode, this engine is capable of performing mechanical work of 2200 joules every second. We denote this power as P1 = 2200 W.
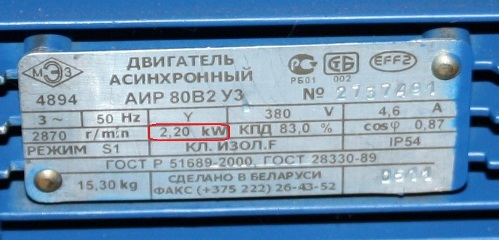
Rated active electric power of an induction motor
To determine the rated active electric power of an induction motor, based on the data from the nameplate, it is necessary to take into account the efficiency. So, for this electric motor, the efficiency is 83%.
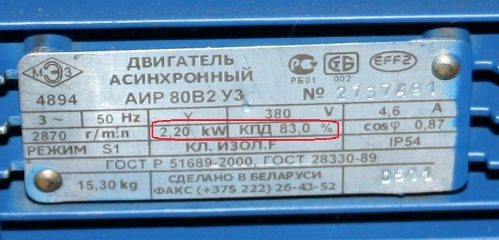
What does it mean? This means that only part of the active power supplied from the network to the stator windings of the motor, and irrevocably consumed by the motor, is converted into mechanical power on the shaft. Active power is P = P1 / Efficiency. For our example, according to the presented nameplate, we see that P1 = 2200, efficiency = 83%. So P = 2200 / 0.83 = 2650 watts.
Rated apparent electric power of an induction motor
The total electric power supplied to the stator of the electric motor from the mains is always greater than the mechanical power on the shaft and more than the active power irrevocably consumed by the electric motor.
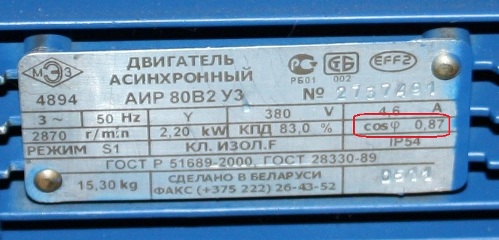
To find the full power, it is enough to divide the active power into cosine phi. Thus, the total power is S = P / Cosφ. For our example, P = 2650 W, Cosφ = 0.87. Therefore, the total power S = 2650 / 0.87 = 3046 VA.
Rated reactive electric power of an induction motor
Part of the total power supplied to the stator windings of the induction motor is returned to the network. it reactive power Q.
Q = √(S2 - P2)
Reactive power is related to apparent power through sinφ, and is related to active and apparent power through square root. For our example:
Q = √(30462 - 26502) = 1502 VAR
Reactive power Q is measured in VAR - in reactive volt-amperes.
Now let's look at the mechanical characteristics of our induction motor: nominal operating torque on the shaft, angular speed, linear speed, rotor speed and its relationship with the frequency of the electric motor.
Rotor speed of an induction motor
On the nameplate we see that when powered by alternating current 50 Hz, the engine rotor performs at a nominal load of 2870 rpm, we denote this frequency as n1.
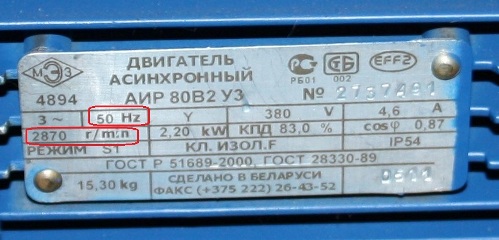
What does it mean? Since the magnetic field in the stator windings is created by an alternating current with a frequency of 50 Hz, for a motor with one pair of poles (which is AIR80V2U3) the frequency of the "rotation" of the magnetic field, the synchronous frequency n, is equal to 3000 rpm, which is identical to 50 rpm. But since the motor is asynchronous, the rotor rotates behind by a slip amount s.
The value of s can be determined by dividing the difference between the synchronous and asynchronous frequencies by the synchronous frequency, and expressing this value as a percentage:
s = ((n – n1)/n)*100%
For our example, s = ((3000 – 2870)/3000)*100% = 4,3%.
Asynchronous motor angular speed
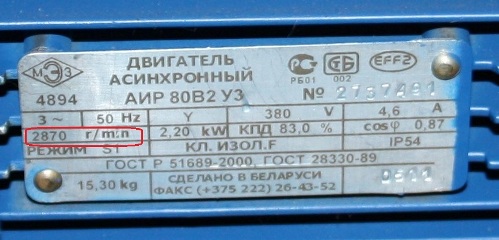
The angular velocity ω is expressed in radians per second. To determine the angular velocity, it is enough to translate the rotor speed n1 into revolutions per second (f), and multiply by 2 Pi, since one full revolution is 2 Pi or 2 * 3.14159 radians. For the AIR80V2U3 engine, the asynchronous frequency n1 is 2870 rpm, which corresponds to 2870/60 = 47.833 rpm.
Multiplying by 2 Pi, we have: 47.833 * 2 * 3.14159 = 300.543 rad / s. You can translate into degrees, for this instead of 2 Pi substitute 360 degrees, then for our example we get 360 * 47.833 = 17220 degrees per second. However, such calculations are usually carried out precisely in radians per second. Therefore, the angular velocity ω = 2 * Pi * f, where f = n1 / 60.
Linear speed of an induction motor
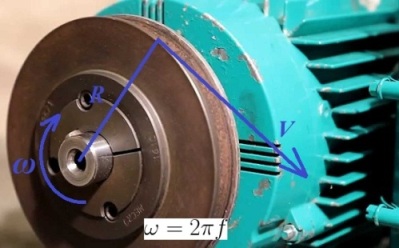
Linear speed v refers to equipment on which an induction motor is mounted as a drive. So, if a pulley or, say, an emery disk of known radius R is installed on the motor shaft, then the linear speed of the point on the edge of the pulley or disk can be found by the formula:
v = ωR
Rated torque of induction motor
Each induction motor is characterized by a rated torque Mn. The torque M is related to the mechanical power P1 through the angular velocity as follows:
P = ωM
The torque or moment of force acting at a certain distance from the center of rotation is maintained for the engine, and with increasing radius, the force decreases, and the smaller the radius, the greater the force, because:
M = FR
So, the larger the radius of the pulley, the less force acts on its edge, and the greatest force acts directly on the shaft of the electric motor.
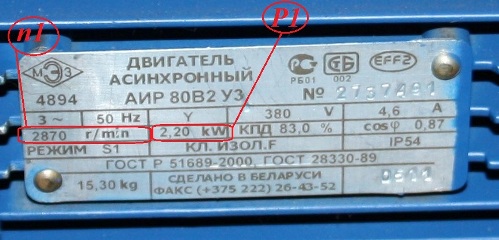
For the AIR80V2U3 engine as an example, the power P1 is 2200 W, and the frequency n1 is 2870 rpm or f = 47.833 rpm. Therefore, the angular velocity is 2 * Pi * f, i.e. 300.543 rad / s, and the nominal torque Mn is P1 / (2 * Pi * f). Mn = 2200 / (2 * 3.14159 * 47.833) = 7.32 N * m.
Thus, based on the data indicated on the nameplate of the induction motor, you can find all the main electrical and mechanical parameters.
We hope that this article helped you understand how the angular speed, frequency, torque, active, useful and apparent power, as well as the efficiency of the electric motor are related.
See also at i.electricianexp.com
: