Categories: Featured Articles » Electrician Secrets
Number of views: 22161
Comments on the article: 2
What technical characteristics of cables and wires are important to consider for reliable operation
It is customary to classify and describe any industrial products, including cable and wire products for power engineering, strictly according to certain criteria, which are called technical characteristics. They allow you to optimally select a specific model from the wide variety of products available, to ensure its long and uninterrupted operation.
Cables and wires created to transmit electrical energy over distances with the least possible loss. In order to most efficiently transfer power from a source to consumers, they are created with:
1. maximum conductivity of conductive lines:
2. the exception of the formation of random, unauthorized ways of draining energy by leakage currents.
Only the simultaneous fulfillment of these conditions makes it possible to reliably and continuously transmit and receive electrical energy.
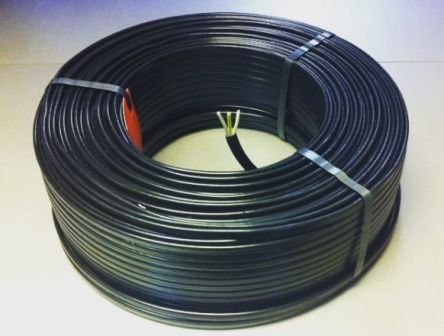
How high conductivity of conductive wires is ensured
Power losses that occur during the passage of currents through metals are directly related to the magnitude of their electrical resistance. They increase with its increase.
To improve the passage of electric current through wires and cables, they reduce the resistance value of their cores due to:
-
selection of material of conductive conductors according to the value of resistivity of metals and alloys;
-
manufacturing a cross section of the core according to the permissible current load;
-
taking into account the temperature of the working environment;
-
the influence of the time flow of technological processes;
-
restrictions on the total length of the electric circuit.
During operation, the state of conductivity and electrical resistance of conductive conductors is constantly monitored by various measuring and protective devices in manual or automatic mode.
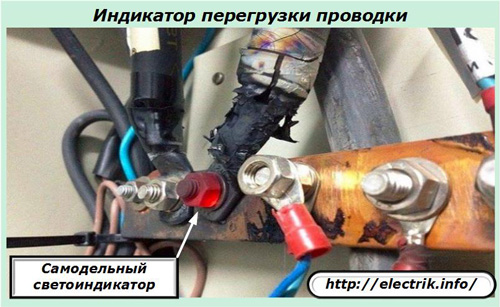
The choice of conductor for the specific resistance of the core material
Recall that this parameter characterizes the electrical resistance of the metal in Ohms, represented by a cylinder 1 meter long and with a cross-sectional area of 1 square meter. It is expressed by the unit of measurement "Ohm ∙ mm2 / m" and amounts to 0.017 for copper, aluminum, steel and brass; 0.026; 0.103; 0.025 Ohm ∙ mm2 / m, respectively.
According to this indicator, copper conductors are used where it is necessary to minimize the current loss to overcome the internal resistance of the circuit. As a rule, they are most often used in cables or power cords with multi-wire cores.
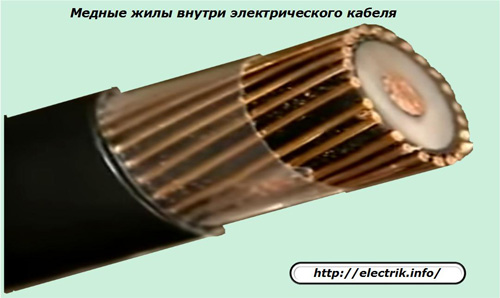
The performance of aluminum and its alloys is slightly worse in conductivity, but they are cheaper to manufacture and have less weight. Therefore, aluminum conductors are used on long highways, which are additionally raised to a great height by means of a special construction of supports and an insulator system.
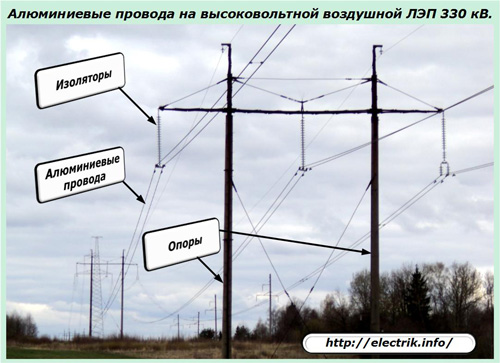
A wire made of steel alloys or brass is added to increase the rigidity and strength of extended routes in order to prevent wire breakage under increased loads created by gusts of powerful wind, snow deposits and other abnormal actions of natural phenomena.
Selection of conductive conductors by cross-sectional area
To carry out electrical calculations in the design of power supply systems, all equipment is created with uniform standardized indicators, summarized in tables.
Veins of wires and cables are made with a calibrated cross-sectional area. For example, for communications and telephone lines, the diameter of the circular cross section of one wire may be 1.2; 0.9; 0.7; 0.64; 0.5; 0.4; 0.32 mm, and for a multi-wire core - from 0.52 to 0.1 mm.
For industrial purposes, produce wires and cables with 1.5 cores; 2.5; 4; 6 mm square and other standardized cross-sectional areas.
The permissible load created by the capacities passing through the cable conductors depends on the metal grade, its cross-sectional area and operating conditions, providing a balance between heating the wire and heat removal to the environment.
By the type of load flowing through the cable, they are classified into:
-
power transmitting electric energy of increased power;
-
control, working in the chains of measurement, protection, automation;
-
controls used for switching automatic devices;
-
communications and telecommunications;
-
other purpose.
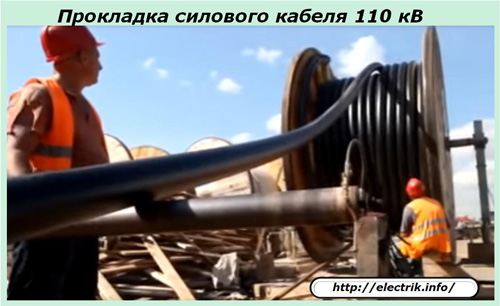
Ways to prevent leakage currents
The movement of electric charges always occurs in a closed circuit from the potential of the generator end to the receiving end of two insulated cores. If you open it, the current stops.
When the dielectric layer is broken between the conductors, part of the current, depending on the transition resistance created, begins to flow through the fault location and can create a short circuit. As a result, there is a useless loss of energy that could be beneficial.
To exclude such cases, bare metal wires on the overhead line are separated from each other by an air gap having the properties of a reliable dielectric.
Conducting conductors are located in cables as close as possible to each other, and the prevention of leakage currents and short circuits is placed on a layer of organic or plastic insulation covering the surface of metal wires.
Its dielectric properties are designed to reliably withstand only a certain level of voltage, which is created between the cores under the load of the cable. If its permissible value is exceeded, then an electrical breakdown of the insulation layer and the leakage current through the place of the defect formed are quite possible.
This feature of the construction of cables and wires dictates the need for their application in strict accordance with the voltage limits for which the insulation is designed. In other words, a telephone cable with copper conductors, for example, 1 mm square, cannot be used for low-current control circuits of 380 or 220 volts even when a large margin of load currents is created. Otherwise, the increased voltage for him will simply break through the insulation layer.
See also:
Cable Insulation Resistance Rating
During installation and operation, cables are subjected to mechanical and thermal loads acting in different directions. To protect against their destructive effects, protection is created - the outer shell or additional armor of various designs.
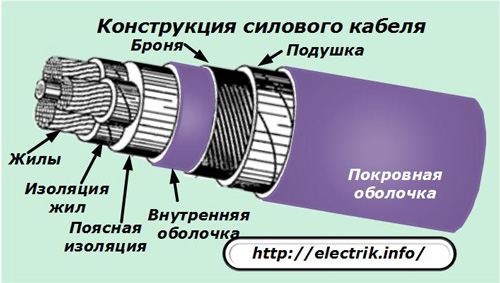
Protective shells are created in a sealed design. They additionally prevent the destructive effect of groundwater, acids and alkalis contained in the soil, where cables are most often placed.
Violation of the tightness of the cable sheath leads to the formation of moisture inside it, which reduces the resistance of the dielectric layer and can cause breakdown of insulation.
An important characteristic of the insulation and cable sheath is its ability to resist fire. Under normal operating conditions, the dielectric layer is only exposed to the operating temperature created by the load. It is not critical to its application.
However, in emergency situations, some materials, such as paper and oil, are subject to fire and are themselves then sources of fire.
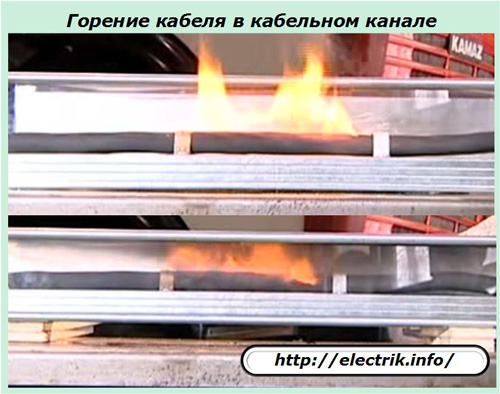
Others, however, may simply not sustain combustion, but melt, collapse from exposure to elevated temperature. Cables with such insulation are called “non-flame retardant” and are marked “ng” in the markings.
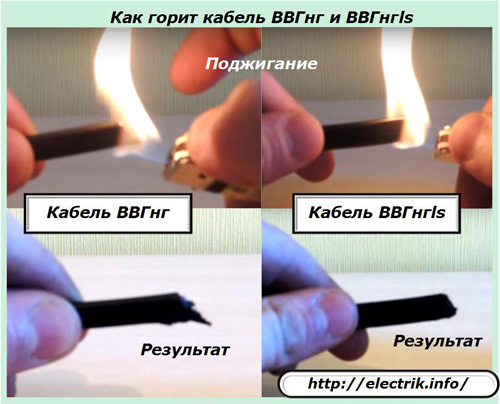
They are divided into two groups that do not support the combustion process when:
1. single gasket:
2. group accommodation.
Engineers of design organizations are involved in the selection of cable products for industrial purposes. Consider how to independently implement this issue for domestic purposes.
How to choose a cable and wire for home wiring
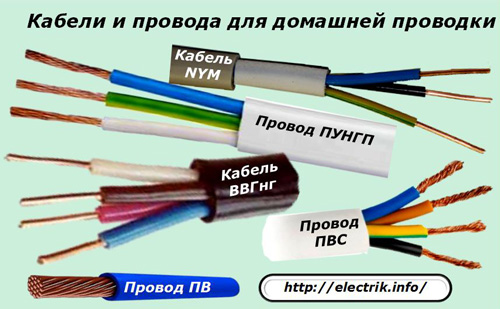
Just note that the old rules that allow the use of aluminum and its alloys for wires and cables of residential buildings are no longer valid. The reason for this: low mechanical stress and tendency to kink during deformation and bending.
For this reason, the old aluminum wires mounted in the Soviet era are gradually refining their resources. In modern wiring, only copper is permitted.
In order not to constantly engage in complex electrical calculations of the correspondence of the wire conductors to permissible temperature heating from leaking loads, the following table has been created.
The ratio of the area of copper wires for permissible load currents and consumer capacities for household wiring.
The range of cable products is very extensive. For domestic purposes are popular:
-
brand wires: PUNGP, PVA; PV;
-
brand cables: NYM; VVGng; VVGngls.
See also on this topic: Types of cables and their differences
See also at i.electricianexp.com
: