Categories: Sharing experience, Home automation
Number of views: 12,660
Comments on the article: 0
Which temperature sensor is better, sensor selection criteria
If this is your first time encountering the issue of choosing a sensor for measuring temperature, then choosing a low-cost and reliable sensor can be an actual problem for you.
First of all, it is necessary to find out the following details: the expected temperature range of measurements, the required accuracy, whether the sensor will be located inside the medium (if not, a radiation thermometer will be needed), the conditions are assumed normal or aggressive, is the possibility of periodic dismantling of the sensor important, and finally, is it necessary graduation is in degrees or it is acceptable to receive a signal that will then be converted into a temperature value.
These are not idle questions, answering which the consumer gets the opportunity to choose for himself a more suitable temperature sensor with which his equipment will work in the best way. Of course, it is impossible to simply and unequivocally give an answer to the question of which temperature sensor is better, the choice remains to be made to the consumer, having first become familiar with the features of each type of sensor.
Here we will give a brief overview of the three main types of temperature sensors (the most common): resistance thermometer, thermistor, or thermocouple. Meanwhile, it is important for the consumer to immediately understand that the accuracy of the obtained temperature data depends on both the sensor and the signal converter - both the primary sensor and the converter contribute to the uncertainty.
Sometimes, when choosing devices, they pay attention only to the characteristics of the converter, forgetting that different sensors will give different additional components (depending on the type of sensor selected), which will need to be taken into account when receiving data.
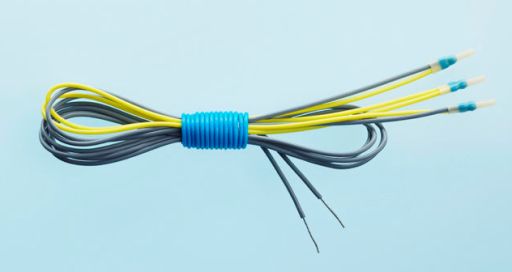
Resistance thermometers - if you need high accuracy
In this case, the sensing element is a film or wire resistor, with a known dependence of the resistance on temperature, placed in a ceramic or metal case. The most popular are platinum (high temperature coefficient), but nickel and copper are also used. Ranges and tolerances, as well as standard dependences of resistance on temperature for resistance thermometers can be found by reading GOST 6651-2009.
The advantage of this type of thermometers is a wide temperature range, high stability, good interchangeability. Particularly resistant to vibration, platinum film resistance thermometers, however, they already have a working range.
Sealed elements of the TS are produced as separate sensitive elements for miniature sensors, however, both resistance thermometers and sensors are characterized by one relative minus - they require a three-wire or four-wire system for operation, then the measurements will be accurate.
And yet, the glaze of the sealing case should be suitable for the selected conditions so that temperature fluctuations would not lead to the destruction of the sealing layer of the sensor. The standard tolerance of platinum thermometers is not more than 0.1 ° C, but individual graduation is possible to achieve an accuracy of 0.01 ° C.
Reference platinum thermometers (GOST R 51233-98) have higher accuracy, their accuracy reaches 0.002 ° C, but they must be handled with care, because they cannot stand shaking. In addition, their cost is ten times higher than standard platinum resistance thermometers.
An iron-rhodium resistance thermometer is suitable for measurements under cryogenic temperatures. The abnormal temperature dependence of the alloy and the low TCR allow such a thermometer to operate at temperatures from 0.5 K to 500 K, and the stability at 20 K reaches 0.15 mK / year.
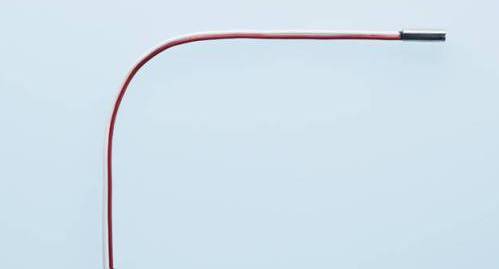
The structurally sensitive element of the resistance thermometer is four pieces of spiral laid around an aluminum oxide tube, covered with pure aluminum oxide powder. The turns are isolated from each other, and the spiral itself is, in principle, vibration-proof. Sealing with specially selected glaze or cement based on the same alumina. A typical range for wire elements is from -196 ° C to +660 ° C.
The second version of the element (more expensive, used at nuclear facilities) is a hollow structure, characterized by very high stability of parameters. An element is wound on a metal cylinder, the surface of the cylinder being covered with a layer of aluminum oxide. The cylinder itself is made of a special metal similar in thermal expansion coefficient to platinum. The cost of hollow element thermometers is very high.
The third option is a thin-film element. A thin layer of platinum (of the order of 0.01 microns) is applied to the ceramic substrate, which is coated with glass or epoxy on top.
This is the cheapest type of element for resistance thermometers. Small size and light weight - the main advantage of a thin-film element. Such sensors have a high resistance of about 1 kΩ, which negates the problem of two-wire connection. However, the stability of thin elements is inferior to wire. A typical range for film elements is from -50 ° C to +600 ° C.
A spiral made of platinum wire coated with glass is an option of a very expensive wire resistance thermometer, which is extremely well sealed, resistant to high humidity, but the temperature range is relatively narrow.
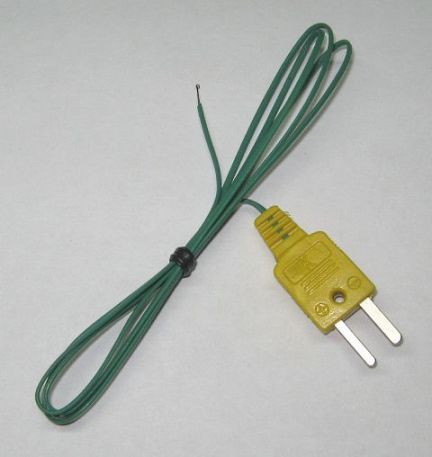
Thermocouples - for measuring high temperatures
The principle of operation of the thermocouple was discovered in 1822 by Thomas Seebeck, it can be described as follows: in the conductor of a homogeneous material with free charge carriers, when one of the measuring contacts is heated, an emf will appear. Or so: in a closed circuit of dissimilar materials, under conditions of a temperature difference between the junctions, a current occurs.
The second formulation provides a more accurate understanding. thermocouple principle, while the first reflects the very essence of thermoelectricity generation, and indicates the accuracy limitations associated with thermoelectric heterogeneity: for the entire length of the thermoelectrode, the decisive factor is the presence of a temperature gradient, so immersion in the medium during calibration should be the same as the future working sensor position.
Thermocouples provide the widest operating temperature range and, most importantly, have the highest operating temperature of all types of contact temperature sensors. The junction can be grounded or brought into close contact with the studied object. Simple, reliable, durable - this is about a sensor based on a thermocouple. Ranges and tolerances, thermoelectric parameters of thermocouples can be found by reading GOST R 8.585-2001.
Thermocouples also have some unique disadvantages:
-
the thermoelectric power is nonlinear, which creates difficulties in the development of converters for them;
-
the material of the electrodes needs good sealing due to their chemical inertness, because of their vulnerability to aggressive environments;
-
thermoelectric heterogeneity due to corrosion or other chemical processes, due to which the composition changes slightly, forces to change the calibration; the large length of the conductors gives rise to the effect of the antenna and makes the thermocouple vulnerable to EM fields;
-
The insulation quality of the transmitter becomes a very important aspect if low inertia is required from a thermocouple with a grounded junction.
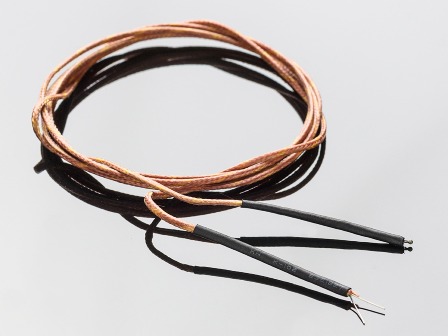
Noble metal thermocouples (PP-platinum-rhodium-platinum, PR-platinum-rhodium-platinum-rhodium) are characterized by the highest accuracy, the least thermoelectric heterogeneity than thermocouples of base metals. These thermocouples are resistant to oxidation, therefore they have high stability.
At temperatures up to 50 ° C, they practically give an output of 0, so there is no need to monitor the temperature of cold junctions. The cost is high, the sensitivity is low - 10 μV / K at 1000 ° C. Inhomogeneity at 1100 ° С - in the region of 0.25 ° С. Contamination and oxidation of the electrodes create instability (rhodium is oxidized at temperatures from 500 to 900 ° C), and therefore electrical inhomogeneity still appears. Pairs of pure metals (platinum-palladium, platinum-gold) have better stability.
Thermocouples that are widely used in industry are often made of base metals. They are inexpensive and vibration resistant. Especially convenient are electrodes sealed with a cable with mineral insulation - they can be installed in difficult places. Thermocouples are highly sensitive, but thermoelectric heterogeneity is a disadvantage of cheap models - the error can reach 5 ° C.
Periodic calibration of equipment in the laboratory is pointless; it is more useful to check the thermocouple at the place of installation. The most thermoelectrically inhomogeneous pairs are nisil / nichrosil. The main component of uncertainty is taking into account the temperature of the cold junction.
High temperatures of the order of 2500 ° C are measured by tungsten-rhenium thermocouples. It is important here to eliminate oxidizing factors, for which they resort to special sealed inert gas covers, as well as to molybdenum and tantalum covers with insulation with magnesium oxide and beryllium oxide. And of course, the most important area of application of tungsten-rhenium is thermocouples for nuclear energy under neutron flux conditions.
For thermocouples, of course, a three-wire or four-wire system will not be required, but it will be necessary to use compensation and extension wires, which will allow the signal to be transmitted 100 meters to the measuring equipment with minimal errors.
Extension wires are made of the same metal as the thermocouple, and compensation (copper) wires are used for noble metal thermocouples (for platinum). Compensation wires will become a source of uncertainty of the order of 1-2 ° C with a large temperature difference, however, there is an IEC 60584-3 standard for compensation wires.
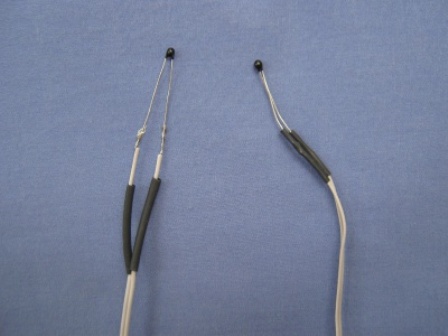
Thermistors - for small temperature ranges and special applications
Thermistors They are peculiar resistance thermometers, but not wire ones, but sintered in the form of multiphase structures, based on mixed transition metal oxides. Their main advantage is small size, a variety of various forms, low inertia, low cost.
Thermistors come in negative (NTC) or positive (PTC) temperature coefficient of resistance. The most common NTC, and RTS are used for very narrow temperature ranges (units of degrees) in monitoring and alarm systems. The best stability of thermistors is in the range from 0 to 100 ° C.
Thermistors are in the form of disk (up to 18 mm), bead (up to 1 mm), film (thickness up to 0.01 mm), cylindrical (up to 40 mm). Small thermistor sensors allow researchers to measure temperature even inside cells and blood vessels.
Thermistors are mainly in demand for measuring low temperatures due to their relative insensitivity to magnetic fields. Some types of thermistors have operating temperatures up to minus 100 ° C.
Basically, thermistors are complex multiphase structures sintered at a temperature of about 1200 ° C in air from granular nitrates and metal oxides. The most stable at temperatures below 250 ° C are NTC thermistors made of nickel and magnesium oxides or nickel, magnesium and cobalt.
The specific conductivity of a thermistor depends on its chemical composition, on the degree of oxidation, on the presence of additives in the form of metals like sodium or lithium.
Tiny bead thermistors are applied to two platinum terminals, then coated with glass.For disk thermistors, the leads are soldered to the platinum coating of the disk.
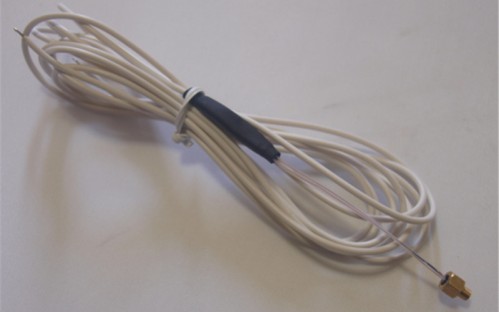
The resistance of thermistors is higher than that of resistance thermometers, usually it lies in the range from 1 to 30 kOhm, so a two-wire system is suitable here. The temperature dependence of the resistance is close to exponential.
Disk thermistors are best interchangeable for a range from 0 to 70 ° C within an error of 0.05 ° C. Bead - require individual calibration of the transducer for each instance. Thermistors are graduated in liquid thermostats, comparing their parameters with an ideal platinum resistance thermometer in steps of 20 ° C in the range from 0 to 100 ° C. Thus, an error of not more than 5 mK is achieved.
See also at i.electricianexp.com
: