Categories: Featured Articles » Electrician Secrets
Number of views: 46863
Comments on the article: 13
How to distinguish a good self-clamping terminal block from a fake
There are several ways to connect the conductors of wires and cables. Each of them is characterized by its advantages and disadvantages. Recently, a way of connecting conductors with the help of terminal blocks wago. Many people prefer this method of connecting conductors due to such an advantage as ease of connection.
Using these terminal blocks, the process of wiring is greatly simplified: to connect the conductors, you do not need a special tool, nor do you need special skills and experience in conducting electrical work.
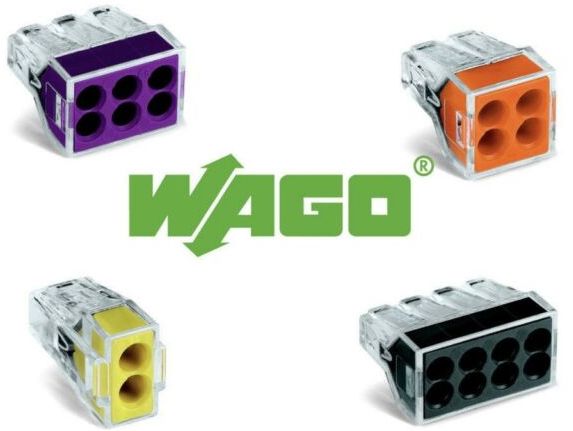
Wago terminals come in several series, each of which has its own design features and method of clamping conductors. The easiest to install are the Wago 773 series self-clamping terminals and the more compact 2273 series terminals. To connect the conductor to the self-clamping terminals, you need to strip it and simply insert it into the terminal block hole until it stops. Contact connection is ready.
As for reliability, judging by customer reviews and test results, it follows that these terminals fully comply with the declared characteristics, namely the rated load current. But it often happens that the wiring installed using these terminal blocks fails.
The main reason is the use of non-original terminal blocks, fakes that do not withstand the specified load current and for this reason fail. How to distinguish a good self-clamping terminal block from a fake?
Firstly, it is necessary to buy terminals exclusively from Wago official representatives and distribution partners. In order to find out the address of the store in your city, you need to go to the official Wago website and see a list of distribution partners in a particular city.
If your city does not have Wago partners, then it is highly likely that in stores specializing in the sale of electrical products, you may be sold a fake that does not match the characteristics of the original terminals. How in this case to check the quality of the terminals?
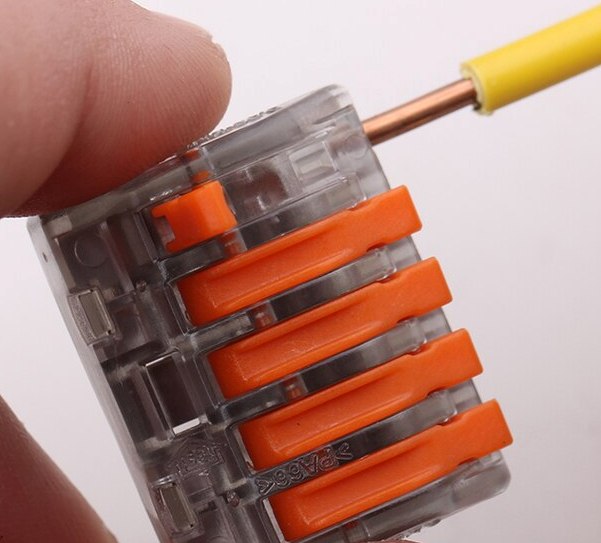
First of all, it is necessary to turn to the terminal housing. The following data should be shown on it: series, range of acceptable values of the connected conductors, the length of stripping of the connected conductor from insulation, as well as the Wago logo. In addition, the indicated data must correspond to the ones declared by the manufacturer for one or another terminal block of the series.
Therefore, before purchasing the terminals, it is recommended to go to the official website of the manufacturer and select the necessary terminal blocks of a particular series and their corresponding parameters, as well as color, in the product catalog.
You should also pay attention to the presence in the terminals of the test holes characteristic of the original product for test leads, windows for checking the sufficiency of stripping the insulation from the connected conductor.
In addition, the part of the case of the self-clamping terminal block must be transparent so that when connecting the conductors, you can visually verify the reliability and correctness of the contact connection.
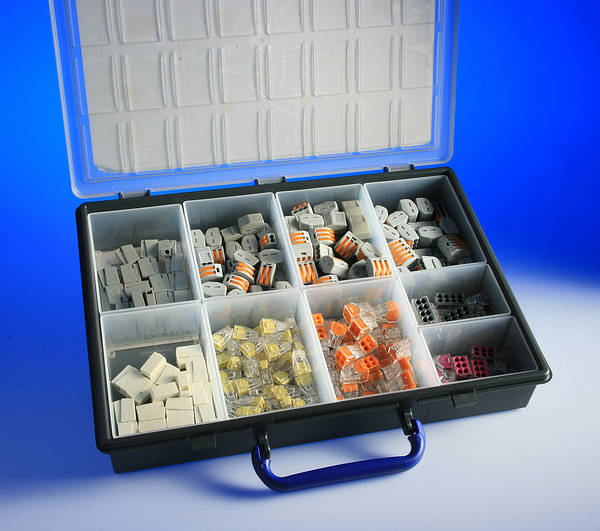
If the type of self-clamping terminal block provides for the connection of aluminum conductors, then you need to make sure that it contains a special Alu-Plus paste, which removes the oxidation film from the connected aluminum conductors, and also prevents its reappearance during operation contact resistance.
The above recommendations regarding the selection of original products are subjective, since it is possible to draw a conclusion about the reliability of the terminal strip only on the basis of personal experience in its operation or when conducting appropriate electrical tests.
In addition to the above, it should be noted that the reliability of contact connections of electrical wiring made using self-clamping terminal blocks can be ensured only subject to the rules and recommendations for connecting and operating a particular type of terminal. Therefore, very often an erroneous conclusion is made about the unreliability of the terminals, and in fact the reason for their damage was their incorrect connection or the lack of proper protection of the wiring section from possible overloads.
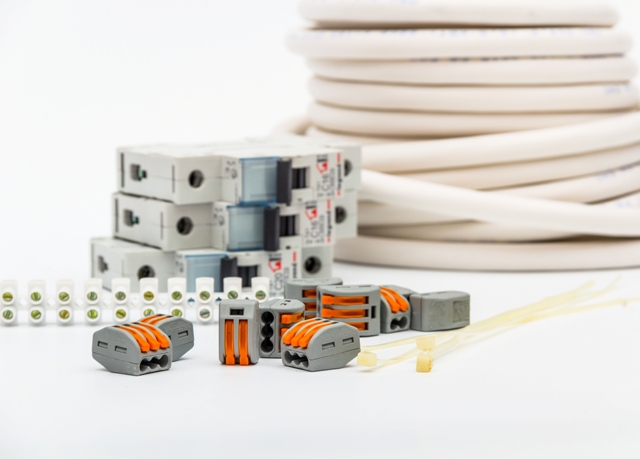
See also at i.electricianexp.com
: