Categories: Sockets and switches, Electric installation work
Number of views: 61538
Comments on the article: 5
Features of mounting sockets and switches on various surfaces
Industrial and residential wiring is carried out in one of two ways of laying:
1. hidden inside wall structures;
Under each of these types, junction boxes, sockets and switches are also available, which are also called electrical points or network connection nodes.
During their installation, many home masters focus on the design of the room and ease of use. However, it is worth considering such requirements for electrical characteristics as:
-
reliable contact joints providing high-quality transmission of electricity with minimal voltage losses;
-
durable electrical insulation of live conductors and structural elements under the potential of the network;
-
safety of operation, including ease of use, restriction of access, fire protection.
Installation of sockets and switches in hidden wiring
Walls of concrete slabs, bricks, foam concrete
In old Soviet-built houses, void channels and outlet openings were created inside the walls for mounting switches and sockets. They wired and installed metal boxes mounted with a solution of concrete or alabaster after cable winding.
When the mortar firmly grasped the installation box, a socket was inserted into it and the screws of the sliding tabs installed in the spacer bracket securely fixed the housing. In this way, the socket was fixed inside the wall through the installation box and solidified concrete.
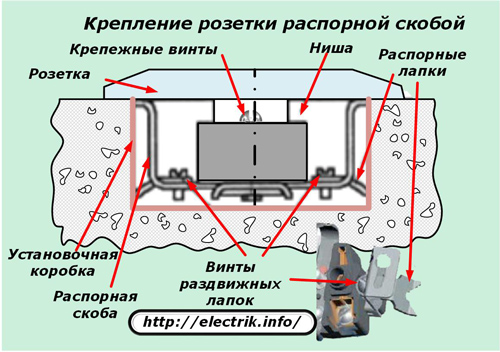
The internal mounting of the circuit breaker was also carried out according to this proven technology for decades. On it, switches with sockets are fastened now. It was only instead of metal boxes that plastic non-combustible materials based on high-strength grades of foam began to be used, which have good dielectric properties and are resistant to fire.
In addition, with the expansion of the sliding tabs in a dense plastic case, a strong connection is created that securely holds the socket in the wall. When the box is metal, it provides less friction (better sliding on the created surfaces) and withstands mechanical loads worse.
For this reason, old outlets are often pulled out of the installation boxes, creating a pre-emergency situation.
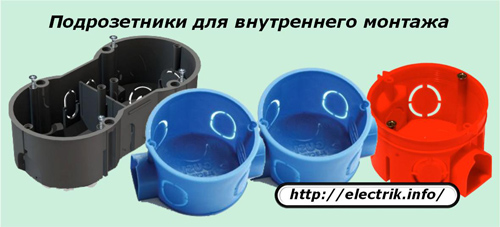
Now many apartment owners are replacing obsolete electrical wiring or laying new ones on their own in buildings under construction. Often there are cases when the walls of concrete, brick, foam blocks do not have internal cavities for mounting cables and wires.
In this case, you can lay open wiring, which is usually done in technical rooms or do wall chipping. When choosing hidden wiring, you will need to create recesses in the wall for installing the socket. The main stages of this work are described in detail in the article. “How to install the box under a wall outlet or switch inside the wall”.
Now residents have a lot of electrical appliances, and there may not be enough sockets to use them. Therefore, it is customary to install not one, but several outlets assembled in consecutive blocks. For their installation, special sockets are used, as shown in black in the figure. You can also dial a design of single modules that are inserted one into the other. This option is shown in the picture in blue boxes.
After the installation hole for one or more outlets is ready, a socket box with a wired cable is inserted into it and fixed with a mortar.
When the mixture hardens and allows you to mount the socket, then it can be fixed with the same spacer with sliding tabs-clamps. In addition to this method, there are sockets for screw mounting of the internal contact mechanism on modern socket boxes. This allows you to choose the best installation option.
Fastening of the mechanisms of sockets and switches with self-tapping screws is noted for increased reliability and strength.
Walls covered with ceramic or gypsum tiles
It is quite difficult to install a socket or switch inside the wall when it is already glued with ceramic tiles. In this case, there is a high risk of damage to brittle surfaces. Many electricians simply refuse such work, not wanting to mess with fragile material that can crack in the most unexpected place.
However, this work may well be done if you use a special tool and exercise caution. The technology provided by photos allows you to install the outlet on a ceramic tile. Just keep in mind that inside the wall in the selected place there is a cavity for laying the cable or the old wiring is laid.
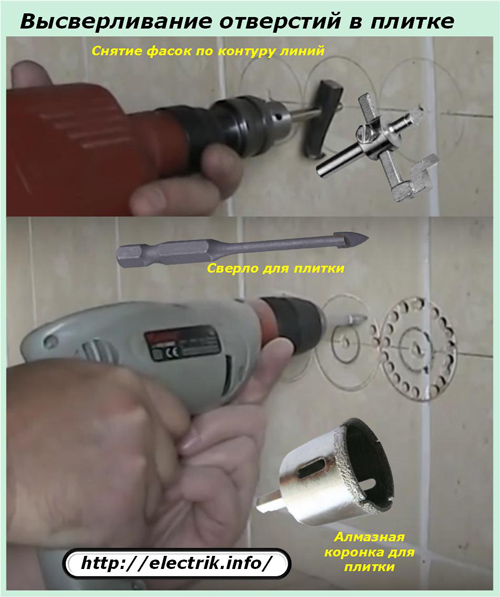
Holes in ceramics can be drilled with special drill bits or a diamond-coated crown. However, it is better to acquire the latter for permanent professional work because of its cost. And several outlets can be installed in the tile with a drill, creating holes along the perimeter of the circle, as shown in the photographs.
Initially, you will need to mark on the tile with a pencil, ruler and compasses, taking into account the horizon. Then the centers are drilled on it and the chamfers around the circle are removed with the help of a ballerina drill.
After the drilling work is completed, they begin to knock out excess pieces with hammer blows on the chisel, chisel or chisel. In this case, accuracy of actions is important when it is necessary to limit the impact force due to the fragility of ceramics. A sharpened blade will easily chamfer the edges and prevent the creation of deep cracks that extend beyond the marked area.
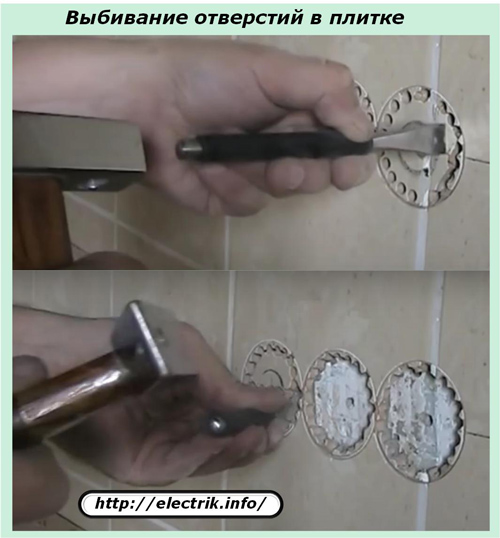
When the inner space of the tile is removed by the cutting edges of the chisel, you will immediately need to align its walls. To do this, use an emery wheel, driven into rotation by a conventional drill.
Next, you will need:
-
drill holes in the freed concrete under the installation box. At the same time, it is important not to touch the edges with the already worked edges in ceramics;
-
drill concrete under the tile first with a small diameter drill, and then expand it with a large one. It is not recommended to use a thick drill immediately because of the increased loads that will be transferred from the concrete wall to the ceramic tile;
-
remove excess concrete between the holes with an electric chisel, as shown in the bottom photo. You can work with a hand tool.
During these operations, it is better to use a professional hammer drill. An impact drill will also cope with such loads, but the whole process will take some time and will require a lot of effort.
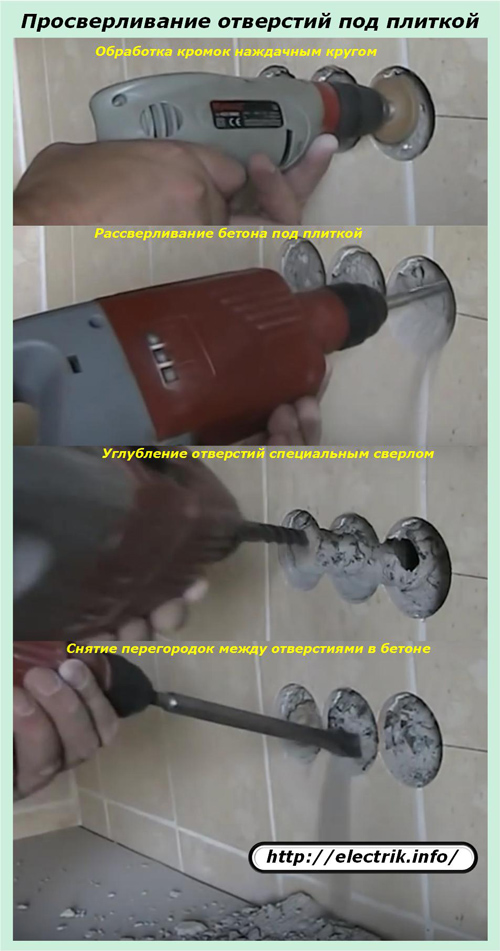
After all the excess concrete is selected to install the box from this place, you need to drill a hole to the inner cavity into which the cable will be laid and run it into this highway. If the box is installed in place of the old outlet, then this task is greatly simplified.
After entering the cable, it will be visible in the prepared hole. To capture it, a simple home-made hook from a small piece of soft wire is introduced, inserted behind the back of the cable.
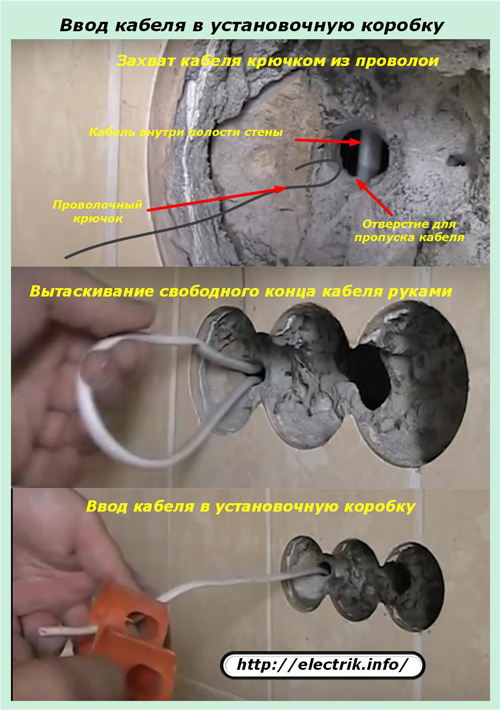
Next, you will need to carefully pull the cable out of the hole first with a hook, and then with your hands and insert its free end into the installation box, as shown in the photographs.
Then the remaining wires are inserted into the same box through the made jumpers, and the whole structure is pressed into the cavity cut into the wall, which is filled with mortar. For better fastening of the box, it is recommended to break the safety partitions of the holes in it to fill the insides with excess concrete, which can be easily cleaned before hardening with a piece of cloth.
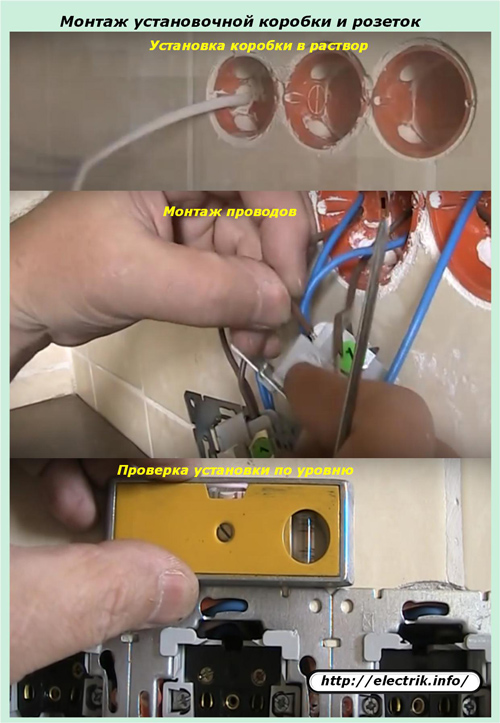
When the putty hardens inside the box, connect the wires to the terminal blocks and assemble the socket mechanism, checking the horizontal installation.
If the installation quality is satisfactory, then a decorative cover is installed on the entire structure and it is fixed with a screw connection.
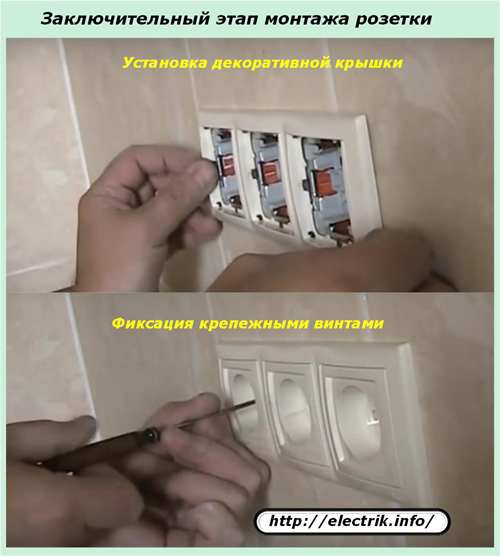
At the same time, it is not recommended to rush to close the covers before conducting electrical checks of the circuit. After all, if a break in the electrical connection is detected, or, even worse, a connection error that creates a short circuit, then they will have to be removed again.
Sometimes electricians forget or do not specifically check the installation before applying the operating voltage to the circuit, hoping in a hurry that the short-circuit occurred should disconnect the circuit breaker protections, and a wire break will appear as an inoperative outlet. Then, they say, and have to look for a malfunction. This is a fallacy that characterizes the low qualifications of performers.
For the outlet to work, you will also need to connect the cable from the back of it. According to all the rules for this, it is necessary to make connections inside the junction boxes or panels. But, after all, this is not always possible or advisable. Especially if a small revision of the scheme is done without violating the design of the premises.
In this case, the most acceptable exception to the rule is chosen - splicing of wires in the internal cavities of the wall. It must be done especially carefully, carefully and reliably. Otherwise, any error will cause a wall to break in order to troubleshoot in the future.
To connect the ends of the wires, they are put on before connecting heat shrink tubing to enhance insulation. Since the metals of the connecting wire can be different, for example, copper and aluminum, steel terminals with screw terminals are used.
Direct connection of such conductors is highly undesirable due to galvanic processes occurring at the contact point. They during prolonged operation lead to the oxidation of external surfaces and an increase in transition resistance.
Wires with cleaned ends are inserted into the terminal and clamped with screws with a force that ensures tight contact, but not violating the integrity of the metal part of the conductor. Then, the prepared heat-shrinkable tube is shifted to the place of joining and heated. If there is no industrial hair dryer, then it is entirely possible to dispense with the flame of a match or a lighter, as shown in the photograph.
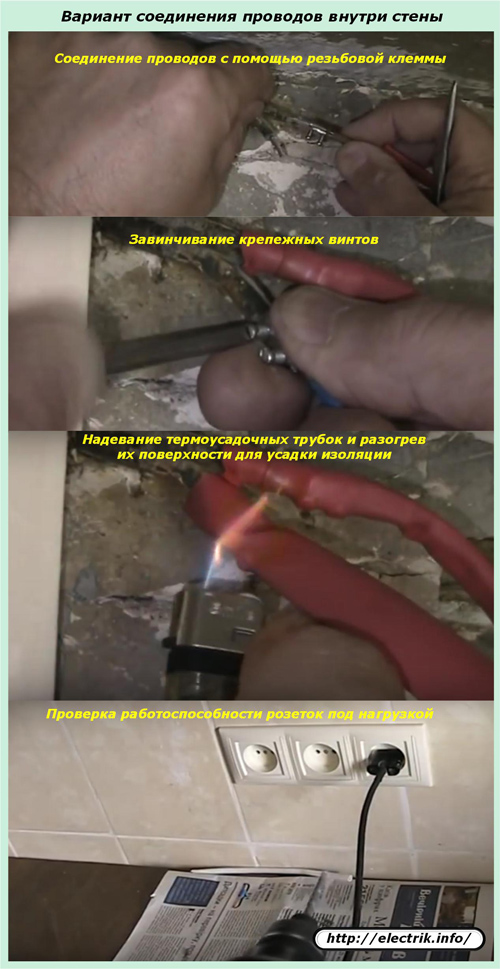
Verification of the assembled structure should not end with the definition of the phase wire by the indicator, but with the test of each new outlet under load. For this purpose, you can use the same drill or hammer that worked. Only a conclusion about operability is made after a control hole has been drilled in any material, for example, a metal corner. Engine idling may not reveal a latent defect, which will manifest much later.
Drywall walls
Installation of sockets and switches inside thin-walled structures made of plywood, drywall, chipboard is carried out identically. A feature of the technology is the method of fixing the installation box on these building structures.
To this end, clamping screws with thrust plates are placed on the outside of the housing of the special socket.
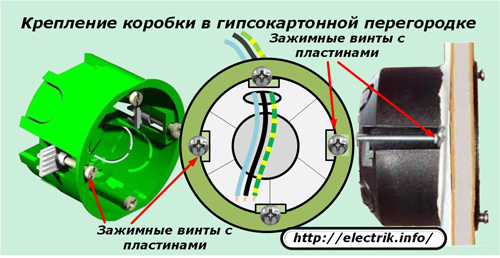
To install such a box in drywall, you need to cut a hole under the box. You can work with an ordinary knife, after training on the wreckage.But, smooth edges and tight edges are provided by a special circular saw - a crown inserted into the drill chuck. With its help, a neat hole is created very quickly.
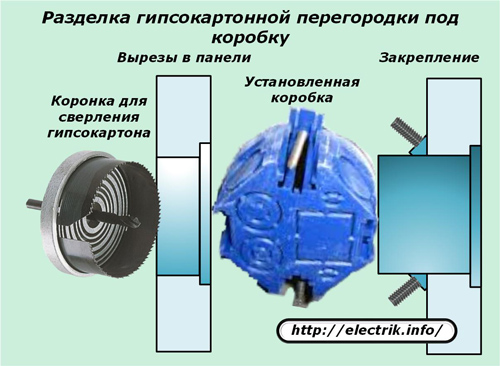
After this, it remains to enter the box into the hole and tighten the screws that secure the locking plates on the inside and tightly clamp the case into the drywall sheet.
Then it remains to enter the cable, cut the ends of the wires and connect the outlet in the usual way.
Installation of sockets and switches in open wiring
In this method of attaching electrical wiring, special attention should be paid to the integrity and strength of the insulation, its ability to withstand the effects of random mechanical loads.
For the installation of sockets for building structures, open wooden sockets are used - special cut-out disks or plates of a rectangular or rounded shape, which are impregnated with a protective fire-prevention compound in the factory.
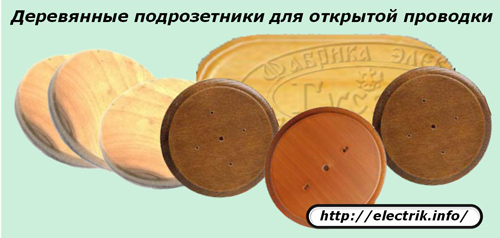
They can also be made of polystyrene, getinaks and other non-combustible materials with dielectric and heat-insulating properties with a plate thickness of about 1 cm.
They are fixed on the wall with screws with a head under the "sweat" or glued. On wood and other materials capable of fire in the event of a malfunction in the wiring, additional protection is installed with a thickness of about 3 mm from the gaskets of paronite.
The case with the mechanism of the socket or switch is mounted to the installed socket box with the top cover removed with two ordinary screws with semicircular heads. If you use secret models, then their conical end during twisting will crash into the hole and begin to push apart, wedge the material of the case and eventually split it.
And when such fasteners are not tightened, then the housing of the socket together with the mechanism will become loose and as a result simply breaks down. Therefore, screws are used for fastening, pressing the case tightly against the undersocket without wedging the material.
But, here you need to make sure that the housing cover does not crush the wires or cable. If this happens, then over time the pinched insulation will break down from the constant mechanical stresses that occur when installing and removing the plug in the contact mechanism. To do this, small areas are broken out in the lids, indicated by plastic membranes - prepresses.
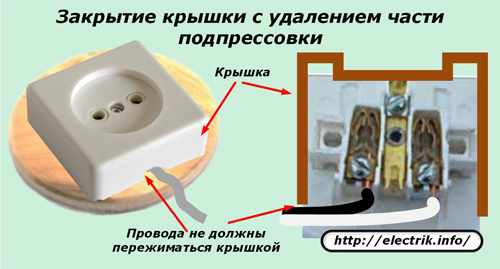
For older sockets and switches, the box lid was more fragile and could crack when removed from the prepress. Therefore, it was preliminarily trimmed with mechanical tools. Modern cases are stronger and tougher. They allow you to remove the jumper by simply cutting the knife. But, to perform this operation without a tool with bare hands is not recommended - you can easily get a finger injury.
See also at bgv.electricianexp.com
: