Categories: Electrician Secrets, Electric installation work
Number of views: 61859
Comments on the article: 8
Why wire twisting is prohibited
According to clause 2.1.21. PUE, connection of wires and cables should be carried out in one of the following ways: by welding, crimping, using screw or bolt connections, or by soldering in accordance with applicable instructions approved in the established manner. As you can see, the "twist" is not mentioned here at all. We can safely conclude: twisting is practically prohibited by PUE.
However, let's see why the official attitude to twisting is so unambiguous, what could be the reason for its exclusion from the list of permitted methods of connecting wires, because it is completely clear that this was done for a reason. Allowed: crimping, soldering, welding and screw connection. To begin with, we will consider what are the features of the allowed connection methods, and what is their difference from twisting.
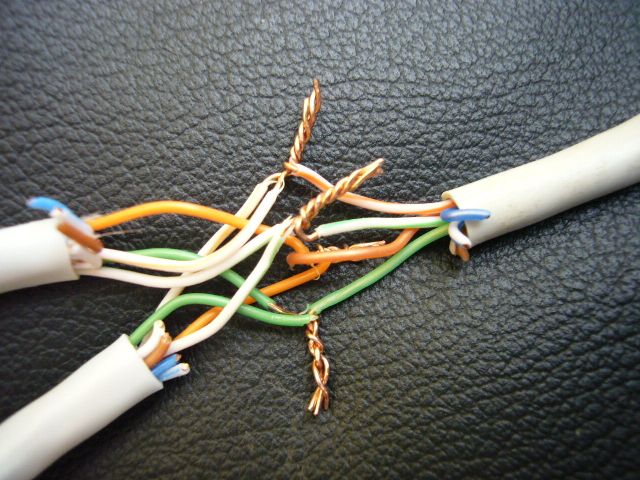
Soldering and welding
Soldering and welding require solidity and the maximum possible conductivity of the created permanent connection. During soldering, the one-piece compound formed is formed by interatomic bonds, because when the metals being joined are heated below their melting point, the solder is already molten, it immediately moistens them and flows into the gap, after which it crystallizes.
Welding also involves the establishment of interatomic bonds between the parts to be welded, but here the metals themselves already melt or undergo plastic deformation (or undergo both melting and deformation).
One way or another, it’s now clear to us that both soldering and welding the wires make their pairing as complete and high-quality as the wires combine at the atomic level, which means they are turned into a single wire for the current, when there are no air gaps in the transition between the parts to be joined, there are no extra intermediate elements that can somehow worsen the conductivity.
Crimping and screw connection
As for crimping and screw connection, here it is implied that the mating conductors are so strongly pressed against each other that the quality of the connection is almost identical in terms of conductivity to the welded joint or junction.
Yes, the tensile strength of such a connection may be less than that achieved by welding or soldering, however, the achieved conductivity of the joint is almost as possible as the wires can be said to flow into each other, their metals diffuse. There is not even an intermediate element — solder, whose specific resistance can, in principle, be greater than the specific resistance of the metals of the wires being joined.
If the purpose of the connected wires is such that the wires will not bear significant mechanical load, then crimping or screw connection in conductivity will not yield to welding and soldering.
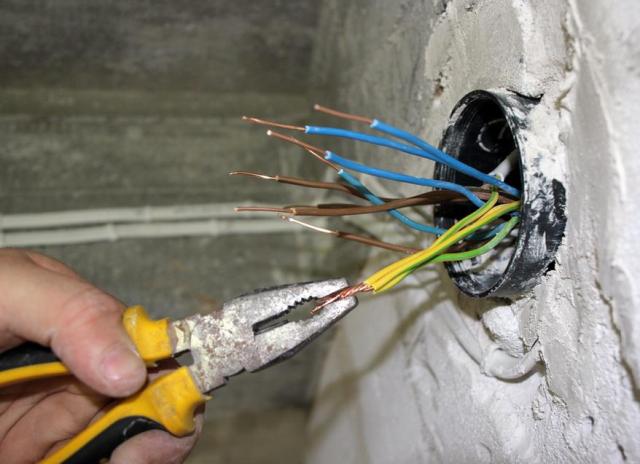
Why is twisting heated
What about twisting? Twisting will not only prevent a reliable, well-conducting contact, it will also not provide strength and will heat up more than the rest of the wire when any significant current passes through it.
This will happen because in the place of twisting the wires are not connected at the atomic level, they just contact a part of their surfaces, and in some places between them there are air gaps in which oxides will necessarily form over time.
In addition, the mechanical twist will still unravel over time, which will further aggravate high resistance problem and the formation of oxidation products.
In the end, due to the combined action of these factors, the contact of the wires in the twist will deteriorate so much that it will be fraught with the formation of sparks and even a fire in the insulation of the wires.
Of course, if we are talking about a temporary connection of wires, for example, during testing of a load switching circuit or when checking part of some repaired device, then in these cases no one will forbid you to use elementary detachable joints - twists.
Nevertheless, one should keep in mind the obvious shortcomings of such a solution as twisting and the inevitable long-term consequences of its use. Therefore, please, make one-piece connections only by methods approved by the PUE.
See also at bgv.electricianexp.com
: