Categories: Novice electricians, How does it work, Industrial electrician
Number of views: 45047
Comments on the article: 2
The device and principles of operation of the magnetic starter
In the name of this electrical device for electrical installations of 0.4 kV, two fundamental actions are laid down at once:
1. actuation as an electromagnet from the passage of electric current through the coil of the coil;
2. start-up of the electric motor by power contacts.
Structurally, any magnetic starter consists of a stationary part and a movable armature that moves along the runners. It is highlighted in blue in the picture.
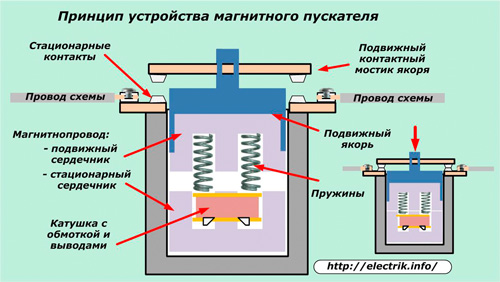
How the electromagnetic system works
The starter can be very simplified as one button, on the case of which there are terminals with connected power circuits and stationary contacts. A contact bridge is mounted on the moving part. Its purpose:
1. providing a double break in the power circuit to turn off the power of the electric motor;
2. reliable electrical connection of the incoming and outgoing wires when the circuit is switched on.
With manual pressure on the anchor, the compression force of the built-in springs is well felt, which must be overcome by magnetic forces. When the anchor is released, these springs drop the contacts to the off position.
This method of manual control of the starter during the operation of the circuit is not used, it is used for checks. During operation, the starters are controlled only remotely due to the action of electromagnetic fields.
For this purpose, a coil winding with coils wound around it is placed inside the housing. It connects to a voltage source. When current is passed through the turns around the coil, a magnetic flux is created. To improve its passage, a laden steel magnetic circuit was created, cut into two parts:
-
the lower half fixed in the device case;
-
movable, which is part of the anchor.
In a de-energized state, there is no magnetic field winding around the coil, the anchor is thrown by the energy of the springs from the stationary part up. Under the influence of magnetic forces arising after the passage of electric current through the winding, the armature moves down.
Drawn to the fixed part of the magnetic circuit, its movable half creates a single structure in the complex with minimal magnetic resistance. Its value during operation is affected by:
-
violations of adjustments;
-
corrosion of steel parts of the magnetic circuit and its fastening;
-
surface wear;
-
technical condition of the springs, their fatigue;
-
defects of a closed loop of the magnetic circuit.
The movement of the anchor inside the hull is limited by two boundary values. In the lower attracted position, a reliable clamping of the contact system must be created. Its weakening leads to burning of the contacts, increasing the value of the transient electrical resistance, excessive heating and subsequent burning of the wires.
An increase in the magnetic resistance of the magnetic circuit for any reason is manifested by an increase in noise due to the appearance of vibrations, which lead to a weakening of the clamp of the contact system and, as a result, to failure of the magnetic starter.
How the power contact system works
Structurally, power contacts are designed for reliable and long-term operation. To do this, they:
-
made of alloys of technical silver deposited by special methods on copper lintels;
-
created with a margin of safety;
-
made in a form that provides maximum electrical contact when turned on and can withstand the electric arc that occurs when the load breaks.
Three-phase circuits use magnetic starters with three power and several additional contacts that repeat the position of the armature and are used in motor control circuits. All of them are drawn on the diagrams in the position corresponding to the absence of current in the coil and the expanded state of the springs.
The control contacts, when the starter is triggered, close (called "closing") or, conversely, open the circuit. In an drawn position, they create a point in the form of a point. For this, the stationary part is made by a plane or sphere (in critical nodes), and the movable part is made by a sphere.
Power contacts are more responsible, must withstand increased loads. They are made to create a contact line consisting of many points. For this purpose, the stationary part is performed by a plane or cylinder, and the movable part - only by the cylinder.
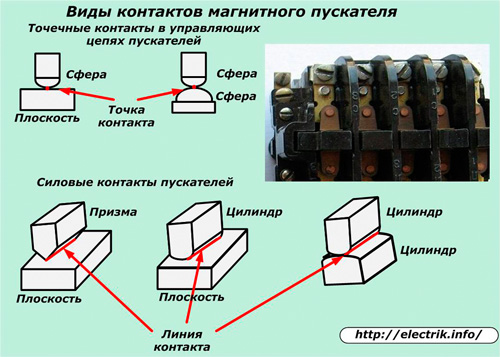
Magnetic starters, manufactured by domestic manufacturers, are classified according to the possibilities of working with loads of different capacities into 7 groups and are designated by increasing value from zero value with switching current up to 6.3 amperes inclusive and up to the sixth - (160 A).
Starters manufactured by foreign manufacturers are classified according to other criteria.
Electricians servicing magnetic starters and supervising their work are required to control the quality of the contact pads and their cleanliness. The current view is that “Contacts of modern starters are made reliably and you can not inspect them” not quite right.
The cleanliness of your contacts depends on many factors, including:
-
load mode;
-
switching frequency;
-
environmental conditions.
All of them appear differently on each specific device. Therefore, they must be periodically monitored and washed with alcohol at the first sign of pollution. When he is not there to perform such work, they use an ordinary school eraser, which, cleaning the metal, leaves its crumbs on the external surface, which have dielectric properties.
They are removed by wiping the surfaces with thin dried wooden sticks from non-resinous varieties of trees. Best suited for these purposes:
-
oak;
-
pear;
-
Apple tree;
-
maple.
Hardwood when wiping contacts additionally polishes the treated surface.
Minor burnout of the contact surfaces is removed with home-made crowfills. So in the language of electricians they call flat segments of durable metal plates (usually they are made from broken hacksaw blades for metal), the surface of which is slightly treated with the smallest emery.
Such a tool allows you to remove a very thin layer of burnt metal and bring the contacts into working condition, to maintain their original shape. It is impossible to use fine emery paper and needle files for such purposes. You can quickly break the formed contact line. “Sandpaper” also clogs the work surface with abrasive chips.
Motor start-up circuits with magnetic starters
The simplest controls
Such an engine connection can be made using the picture below.
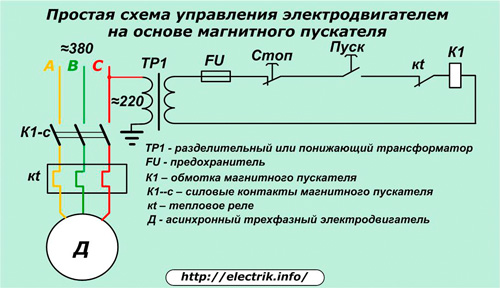
Three-phase power supply ≈380 through the power contacts K1-s is supplied to the electric motor, the temperature of the windings of which is controlled by the thermal relay kt. The control system is powered by any phase and zero. It is acceptable to replace the working zero with a ground loop.
In order to increase electrical safety, a separation or step-down transformer TP1 is used. Its secondary winding cannot be grounded.
The simplest FU fuse protects the control circuit from possible short circuits. When the operator presses the “Start” button, a circuit is created in the control circuit for the current to flow through the winding of the K1 starter, which simultaneously closes its power contacts K1-s.How much time the worker presses the button, so much the engine and works. For the convenience of man, these buttons are mounted with a trigger mechanism.
A running motor with the button pressed can be turned off:
-
removing power on the distribution power board;
-
by pressing the “Stop” button;
-
the operation of the thermal relay kt when the engine overheats;
-
blown fuse.
Such schemes are used where, according to the conditions of technology, it is necessary to keep hands constantly on the equipment and not be distracted from the production process. An example is the work with the press.
The circuit with holding the button contact starter
Adding to the considered circuit only one closing contact of the K1-u starter allows you to put the Start button on the lock with this addition and eliminates its constant pressing. The rest of the scheme completely repeats the previous algorithm.
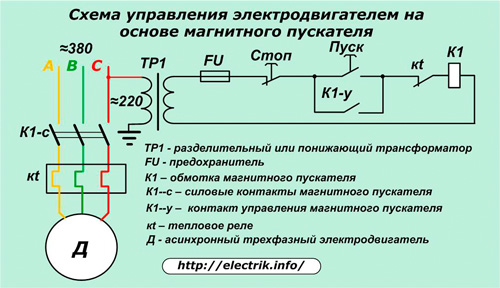
Reverse circuit
Many drive machines require during operation to change the direction of rotation of the motor rotor. This is done by changing the phases of the alternation of the power circuit - by switching the connection points of any two windings on a disconnected motor. In the picture below, the windings of phases “B” and “C” are interchanged. Phase A does not change.
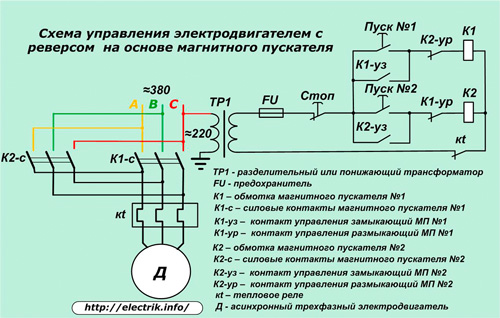
Two magnetic starters No. 1 and No. 2 are already included in the circuit. The engine can only rotate from one of them clockwise or in the opposite direction. For this, an NC contact of the control of the opposite rotation starter is introduced into the control circuit of each winding K1 and K2. It blocks the simultaneous connection of both starters.
To change the direction of rotation of the engine, the operator must:
-
press the stop button. The gap formed by it opens the control circuit and interrupts the passage of current through the working starter. At the same time, the springs drop the anchor, and the power contacts disconnect the voltage from the electric motor;
-
wait for the rotor to stop rotating and press the “Start” button of the next starter. Current will flow through its coil, the button will be held on hold by the make contact, and the winding circuit of the reverse rotation starter will break with the make contact.
Design features of various models
Previously, magnetic starters were equipped with power contacts and one or two of their followers for closing or opening, but modern models are given additional structural elements, due to which they have more features.
For example, complete products from leading manufacturers allow you to perform various control functions for three-phase electric motors, including reversing by incorporating additional equipment into the starter. The consumer can only connect the electric motor and power wires to the purchased module, and the circuit itself is already mounted and adjusted for certain loads.
A promising technical solution is a scheme that allows:
-
untwist the engine rotor to rated speed by connecting its windings according to the "star" scheme;
-
turn on under load when switching to the "triangle".
Cases of magnetic starters can be open or protected from dust and / or moisture by a special shell with seals.
Separate modern models of small capacities mounted on a DIN rail.
Powerful magnetic starters can be equipped with an arc extinguishing system that occurs when current is disconnected by power contacts.
Read also on this topic: What is the difference between a contactor and a starter
See also at bgv.electricianexp.com
: