Categories: Featured Articles » Interesting electrical news
Number of views: 45804
Comments on the article: 5
Heating cables: types and applications
Heating cables - a specific type of cable products that convert electrical energy into heat for heating and perform the function of a receiver of electrical energy, rather than a transmission line. Heating cables are significantly different from ordinary cables and wires, the purpose of which is to transmit electrical energy with the least loss and with a slight voltage drop over the line length (usually not more than 5%).
The heating cable is used as heating sections, i.e. segments of a certain length, and at this length there is a complete drop in the applied voltage. Therefore, the heating section should be considered as a conventional receiver of electrical energy (as one of the types of electric heating elements).
The length of cable heating sections usually ranges from several meters to several hundred meters.
The effect of the dissipation of part of the transmitted energy in the form of heat, which is negative for conventional cables, is used as useful in heating cables. Moreover, the conversion of electrical energy into heat occurs in the most optimal and economical way. The conversion is complete, silent, without the use of additional substances (fuel, oxidizer).
Heating cables have a fairly developed range and are used in a wide variety of installations and devices. But nevertheless they relate to peculiar cable products and in the literature there are practically no works on the design, calculation and use of heating cables.
Types of cables according to the heat dissipation scheme
Resistive linear - heating cables in which heat is released due to the Joule-Lenz effect when electric current passes through the heating core. The cable is designed in such a way that a complete drop in the applied voltage takes place in the heating core, but the cable elements do not overheat above the permissible values.
The length of the heating section is usually from a few to hundreds of meters. Cables of this type may have one, two or more parallel heating cores having a linear or spiral shape. Arbitrary cable cutting along the length is unacceptable.
The thermal power of resistive linear cables decreases slightly during heating, and the magnitude of the change depends on the value of the temperature coefficient of resistance of the material of the heating core. The smallest changes in resistance are observed in alloys of high resistance (TKr + 0.0001), the largest in copper (TKr + 0.004)
Resistive Zonal heating cables do not differ in principle from previous ones, but fundamentally differ in their design. They contain two parallel insulated conductors.
The insulation of conductive conductors has periodically located “windows” displaced from each other with a given step (usually about 1 m). A thin wire coil of high-resistance alloy is superimposed on top of these two cores.
In the "windows" the spiral closes on the conductive wires, as a result, the cable represents a set of resistances (resistors) connected in parallel to the conductive wires. On each of them there is a complete drop in the applied voltage. The zonal cable is convenient in that it can be cut anywhere. The minimum length of the heating section is 1.5 - 2 m.
The maximum length is determined by the cross-section of conductive conductors and linear power.Since the heating element of the resistive zone cables is made of high-resistance alloys, their power is practically independent of temperature, therefore they are also called constant power cables.
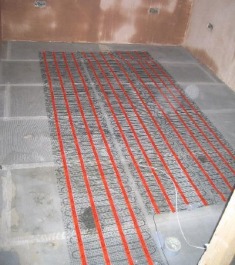
Self-regulating cables have a design partially similar to the design of resistive zone cables. They also contain two parallel conductors, but not insulated. Conductors are either enclosed in a polymer conductive matrix, or connected through spiral polymer conductive threads.
The effect of self-regulation is achieved due to the fact that the fuel element of the cable, made of a polymer conductive material, significantly increases its resistance when heated. The Tcr value of the conductive polymer reaches 0.05-0.075, i.e., 12-18 times more than that of copper.
Inductive Heating Cables in their design they contain ferromagnetic elements, and conductive insulated conductors are laid around the ferromagnetic elements in the form of a winding inducing an alternating magnetic flux in the core. The heat release effect is achieved both due to resistive losses in the winding, and due to resistive losses in the core arising from induced currents.
The ratio of those and other losses is determined by the design of the cable. Losses in the core can be 80-20% of the total cable loss. In the first case, the losses in the winding are small, and it is slightly heated due to its own losses, which allows to obtain a significantly higher linear power compared to resistive cables.
The method of heating pipelines using the "SKIN effect" can also be considered as one of the options for the inductive cable. In this case, the role of the induction winding is played by an insulated core of large cross section, and the role of the inductor is the steel pipe in which this core is located. Heat is generated both in the core and in the pipe due to induced eddy currents.
Applications for heating cables
Devices that use heating cables can be dramatically different in size, operating temperature, and heat output. Therefore, the range of applications for heating cables is very wide.
Heated clothes, blankets, rugs - electric blankets and blankets, heating pads, heated seats, heated clothes and shoes. As a rule, they have a small power (10 - 50 W) and an operating temperature that is safe for humans, i.e. not higher than 50 ° C. This group may include low-power household heaters: baby food heaters, defrosters for refrigerators using heating cables.
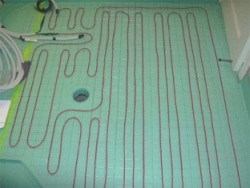
Room heating systems - in them heating cables are used as a fuel element, more or less evenly distributed over the area of the room. If necessary, the cables can be mounted on the walls and on the ceiling. The best option for installing cables in terms of heat transfer, heat storage, safety and security is to install the cable in the thickness of a cement screed, laid under a decorative floor covering.
The temperature on the heated surface is usually 22 - 26 ° C, but can reach 35 ° C. The specific power of floor heating systems varies in the range of 70-150 W / m². Storage systems have power up to 200 W / m². The total power of the system can have very wide limits: from 100 watts to tens and hundreds of kilowatts.
De-icing systems for sidewalks, open stairs, ramps. As in the previous case, the cables are laid in the thickness of the concrete base. These systems function only at a time when snow falls on the surface of these objects or ice forms.
The specific power of heating systems for open surfaces varies in the range of 200-350 W / sq.m. The total capacity of the system ranges from several to tens of hundreds of kilowatts.
This also includes anti-icing systems for sports facilities (football fields, treadmills, racecourses, tennis courts), hazardous sections of highways (ascents, descents, sharp turns), runways. The specific heating power of these systems can reach 500W / sq.m., And the total power - several megawatts.
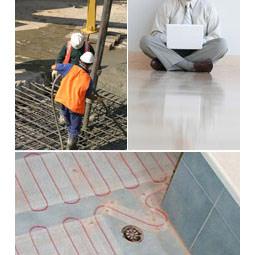
Roof de-icing systems serve to prevent: ice clogging of water flow paths, the formation of icicles and to remove snow and ice from hazardous areas. Heating cables are placed along the water flow paths, in drainpipes, on eaves, water cannons, on valleys and junctions.
The heating cables used in these systems have, as a rule, a linear power of 25 or more watts per meter. The total capacity of the system depends on the design and size of the roof of a particular building and ranges from 1-2 to several hundred kilowatts.
The temperature on the surface of anti-icing systems in the absence of snow and ice and at a negative ambient temperature is usually +5 - 7 ° C. During the melting of snow and ice, the surface temperature is only a fraction of a degree higher than 0 ° C. If the ambient temperature is above + 5 ° С, the anti-icing systems are switched off as unnecessary.
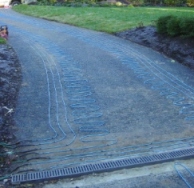
Heating systems for pipelines and tanks. Piping systems are long and branched, and heating cables are the best suited for their heating. In practice, as a rule, there are two types of heating systems - preventing freezing and maintaining the temperature on the pipe above normal (above + 20 ° C). The main purpose of both types of systems is to compensate for heat loss from the pipe (or tank) into the environment.
The heating sections are mounted on top of the pipe (tank) and together closed by thermal insulation. The linear power of heating systems of pipelines is usually 10-60 W / m. The total capacity of the system depends on the length of the pipeline. The specific power of the tank heating systems is 10-80 per 1 sq.m. The heated surface, and the total depends on the size of the tank.
The purpose of anti-freeze systems is to eliminate the formation of ice plugs and rupture of pipelines, therefore it’s enough to maintain + 5 ° C on the pipe. Temperature maintenance systems can vary very much in the required temperature on the pipe (tank): +40 is enough to transport oil and many aqueous solutions ° C, and for bitumen requires 160-180 ° C.
Heating systems for technological equipment They are distinguished by a wide variety of purposes, required temperatures, specific capacities and are developed on the basis of an individual approach.
System purpose
Temperature ° C
Specific power, W / sq.m.
Total power, kW
Thermal barriers in the chambers of industrial refrigerators
2-5
3 - 15
0,5-5
Satellite antenna heating
2-5
200-300
2-15
Degreasing bath heating
30-50
200-400
0,5-3
Heated concrete product lines
40-60
300
20-50
Press plate heating
40-150
300-1000
2-10
Heated cylinders and heads of injection and extrusion machines
120-130
10000 - 20000
Single heater 0.5-2
See also at bgv.electricianexp.com
: