Categories: Featured Articles » Sources of light
Number of views: 3486
Comments on the article: 0
The problem of overheating of lighting LEDs and solutions
When compared with rapidly fading light sources, LED sources have only one, but a very serious flaw. Their durability and reliability largely depend on the efficiency of heat removal from light emitting components. Therefore, the protection circuit of the LED from overheating is an important component of any high-quality LED lighting system.
Average lighting led ten times superior in energy efficiency (profitability) to a traditional light bulb with a filament. However, if the LED is not installed on a radiator of sufficient area, then it will most likely fail quickly. It is generally accepted, without going into details, that more efficient lighting LEDs need more efficient heat dissipation than conventional ones.
Let us nevertheless examine the problem more deeply. We will evaluate two lamps: the first is halogen, the second is LED. And after that - let's pay attention to the ways to preserve the durability of LEDs and extend the life of their drivers. The fact is that the protective part of the LED lighting system should ensure the safe functioning of both LEDs and driver circuits.
For example, we have two lights. Both devices provide 10 watts of light power. The only difference is that a halogen spotlight requires 100 watts of electrical power, and a LED only 30 watts.
We know that LEDs are about 10 times more effective in the light produced, but in reality they are extremely sensitive to high temperatures, and therefore the temperature regime in which the conversion of electric current energy to light is very important for them.
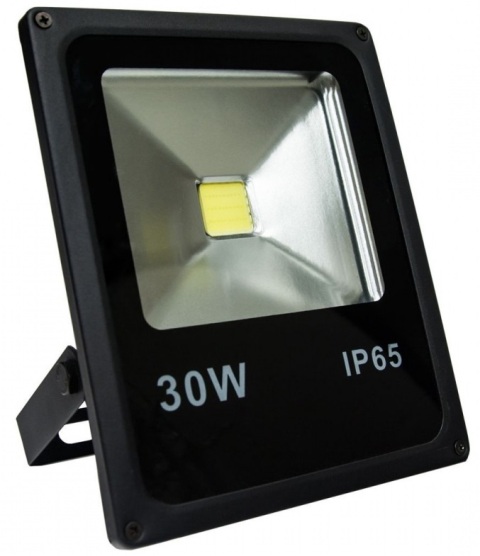
For a luminaire with a halogen lamp, a working temperature even at +400 ° C is a safe norm, while for LEDs, a crystal temperature of +115 ° C is already critically dangerous, and the maximum temperature of the diode case is only +90 ° C. Therefore, the LED must not be allowed to overheat, and there are several reasons for this.
With increasing temperature of the light-emitting transition, the light efficiency of the LED decreases, and this depends both on the design of the LED and on the state of the environment. In addition, LEDs, in principle, differ in the negative temperature coefficient of the direct voltage drop across the junction. This means that with an increase in the transition temperature, the direct voltage drop across it decreases. Typically, this coefficient varies from -3 to -6 mV / K.
Thus, if at 25 ° C the direct voltage drop across the LED is 3.3 V, then at 75 ° C it will already be 3 or less volts. And if the LED driver does not reduce the voltage at all assembly LEDs as the temperature rises, then at one fine moment the current will be maintained inadequately high, which will lead to overheating, overload, a further decrease in the direct voltage drop, and an even faster increase in the crystal temperature. Cheap LED lamps with resistive current limitation often show this disadvantage at the most unexpected moment.
Tolerances for fluctuations in the voltage of the power supply in combination with differences in direct voltage drop on the LED (at the production stage, the LEDs are not ideally identical for this parameter), and due to the negative temperature coefficient of voltage drop - at any time, these factors together can cause a safety violation mode of operation of the LED and provoke a slide to its self-destruction.
Of course, if the design of the LED lamp (especially the radiator) is reliable enough, then short-term brightness drops can be neglected, since they are very rare and these overheats are short-term. But if the overheating is continuous, then the temperature rise immediately turns into a real threat to the lamp.
The reasons for the failure of LEDs when they overheat
LEDs are destroyed by overheating for several reasons. The first reason is a change in the mechanical stress inside the light emitting crystal and the monolithic LED assembly. The second is a violation of tightness, moisture penetration and oxidation. The protective epoxy layer degrades, delamination occurs at the boundaries, and the crystal contacts undergo corrosion.
Third, an increase in the number of dislocations in the crystal leads to a change in the current paths and the appearance of points of excess current density and, consequently, to overheating of these points. Finally - the phenomenon of diffusion of metals at the contacts at elevated temperatures, which also ultimately leads to inoperability of the LED.
LED developers are trying their best to minimize these failure factors, and therefore all the time they are technologically improving the production process. Nevertheless, because of overheating, failures are still inevitable, although they become less common with the improvement of the production process.
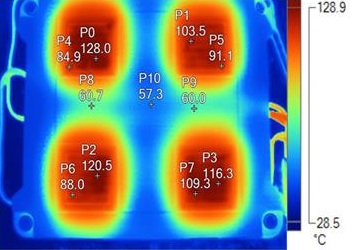
Mechanical pressure is the most common cause of premature failure of LEDs. The bottom line is that with overheating, the sealant softens, the electrical contacts and connecting conductors are displaced from the “factory” position, and when the temperature finally drops, cooling takes place and the sealant solidifies again, but at the same time presses on the already slightly displaced connections, which in the end leads to a clear violation of the initially uniform conductivity. Fortunately, LEDs made without connecting conductors are practically devoid of this drawback.
Soldered joints between the LED and the substrate also experience a similar problem. Regular cyclic, invisible to the eye, softening and hardening end with the appearance of cracks in the solders and the violation of the initial contact. That is why LED failures occur due to an open circuit, and this gap is often not visible. To prevent this problem, you can minimize the difference between the safe operating temperature of the LED and the ambient temperature.
Powerful LEDs (consuming more electrical power) give more light, but their light output is still limited. That is why consumers and manufacturers often have a dangerous temptation to operate the LEDs in the lamp at full power in order to get the maximum possible brightness. But it is really dangerous if you do not provide enough effective cooling.
Of course, designers want to create elegant fixtures of interesting shapes, but sometimes they forget that it is necessary to ensure adequate air movement and adequate heat dissipation - this is often the most important thing for LEDs, following a stable and high-quality power source.
Yes, and the direct installation of LED lights is important. If one lamp is installed above the other as powerful, then the air flow from the lower lamp can be slowed down by the upper one, and the lower one will therefore be in worse temperature conditions. Or, for example, thermal insulation in the wall or on the ceiling of a room can interfere with heat dissipation, even if during the design of the lamp all the thermal calculations were performed perfectly and technologically it was made as correctly as possible. All the same, the probability of failure increases simply due to rash and illiterate installation of the finished product.
One of the worthy solutions to the problem of overheating of LEDs is the inclusion of temperature protection in the driver circuit with feedback precisely by temperature. When the temperature of the emitter for some reason dangerously increased - to lower the power, in order to maintain the temperature within the safe range, the current automatically decreases.
The simplest solution is to add to the schema. positive temperature coefficient thermistor (It is possible with a negative temperature coefficient, but then the circuit should invert the signal in the feedback circuit).
Thermal protection example using a thermistor
For example, consider a circuit based on a specialized microcontroller with a current-limiting circuit. When the temperature rises above a certain threshold (set by a thermistor and resistors), a thermistor with a positive resistance coefficient, mounted on the heatsink together with LEDs, increases its resistance, which leads to a corresponding decrease in current in the driver output circuit.
In this regard, driver circuits with brightness control are very convenient PWM (pulse width modulation), which allows you to simultaneously and manually adjust the brightness, and protect the LEDs from overheating.
A solution with a thermistor is convenient in that a change in current, and hence a decrease in brightness, will occur in such a scheme smoothly, invisibly to the eyes and nervous system, which means that nothing will flicker and will not cause irritation to people and animals around. The temperature of the upper limit is simply determined by the choice of a thermistor and a resistor. This is much better than solutions with temperature sensors, which simply sharply open the circuit and wait until the radiator cools down, and then turn on the lighting again at full brightness.
Specialized LED driver chips, of course, cost money, but the reliability and durability of the lamp obtained in return will repeatedly pay for this investment.
It is worth remembering that, subject to the normal temperature conditions of operation of the LEDs, their service life is measured in tens of thousands of hours, then questions regarding the material costs of the “correct” driver disappear by themselves.
It is only important to provide the driver with a constant low temperature, for this you just do not need to place it close to the radiator of the LEDs. Wrong doing those who strive to seal the placement of components inside the projector. It is better to display the driver housing as a separate unit. Here, safety and prudence are the key to the durability of LEDs.
The best microcircuits for power management of LEDs are equipped with internal circuits for protection against their own overheating in case the microcircuit, for design reasons of the luminaire developer, should nevertheless be located in the same housing with noticeably heating components, such as a radiator. But it is better not to allow the microcircuit to overheat above 70 ° C and equip it with its own radiator. Then both the LEDs and the driver microcircuit will live longer.
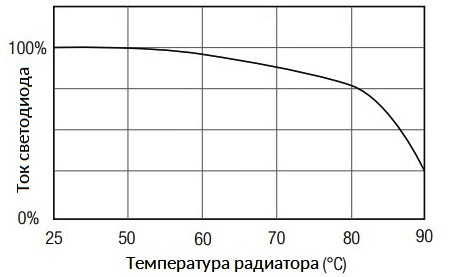
A solution using two series-connected thermistors in a thermal protection circuit may be interesting. These will be different thermistors, since the safe temperature limits for the microcircuit and for the LEDs are different. But the result will be achieved what is needed - smooth brightness control both when the driver overheats, and when the LEDs overheat.
See also at bgv.electricianexp.com
: