Categories: Featured Articles » Electrician at home
Number of views: 116641
Comments on the article: 8
Connection of wires by crimping
Of course, there are so many ways to connect wires. Widely known all terminal blocks: screw and spring, insulated and not. Nut clamps and piercing clamps are popular. Finally, some simply do not pay attention to common rules, preferring elementary twists. And one of the most reliable connections is crimping wire connection.
After crimping, the wire strands cannot be disconnected without cutting them, i.e. this is an integral connection. But it does not need maintenance either. The essence of crimping is reduced to the joint deformation of the connecting cores and the crimping sleeve into which these cores are inserted. The sleeve is compressed, deformed, compresses the cores, microroughnesses on the surface of the metal conductors are in mutual engagement, and is provided reliable electrical contact.
But it only seems that everything is so simple. In fact, there are some subtleties. Here is some of them.
Crimping tool
Most commonly used press tongs (e.g. PMU) with manual or hydraulic drive. Portable hydropresses or even a special cordless tool are less commonly used. Hand clamps are crimped liners with a cross section up to 120 square meters. mm
In the most common case, the working bodies of these tools are dies and punches. In the general case, the punch is a movable element that produces local indentation on the sleeve, and the matrix is a curly fixed bracket that perceives the pressure of the sleeve and deforms it.
It happens that the crimping tool uses interchangeable dies and punches, which should be selected for the nominal cross-section of the sleeve. This is not always convenient. If you are crimping a large number of sleeves of different sections, you have to have with you a pretty weighty set of these same dies and punches, and their constant change can exhaust your nerves. Therefore, for example, pincers are often produced with one, adjustable punch or rotary dies, designed for different sections.
The advantage of such devices is that to configure them for a specific connecting sleeve, you do not need to reinstall anything: just turn the die on the other side or turn the punch screw a few turns.
Separately, it should be noted that some small crimping pliers do not have either dies or punches in their composition, squeezing the sleeves and tips only with curly lips.
It should not be forgotten that an incorrectly selected punch or die can become not only the reason that the wires will not be crimped properly and will fall out of the sleeve. An excessively clamped wire may break off at the junction, and this will happen at the most inopportune moment when the line is already in operation.
Sleeves for pressure testing
You can, of course, use any copper or aluminum tube, but this is extremely undesirable. The difference between electrotechnical metals and common industrial metals is very large, so it is better to use as crimping sleeves special sleeves GM and GA from electrical copper and aluminum, respectively.
Aluminum continuous wires of small cross-sections (up to 10 sq. Mm.) Are connected GAO sleeves with a total wire cross section of not more than 32.5 square meters. mm To connect copper and aluminum conductors, you can use GAM alumina sleeve or GML tinned copper sleeve. The cross section of all these sleeves varies from 10 to 300 square meters. mm At the same time, another advantage of factory sleeves is that their length optimally corresponds to the cross-section according to the conditions of joint strength.
Crimping technology
Crimping can be done by local indentation or continuous compression. Continuous compression is usually performed in the form of a hexagon.
Since aluminum conductors are prone to almost instantaneous formation of an oxide film of low conductivity, the surface of aluminum sleeves and wires must be cleaned to a shiny metal before crimping and treated with quartz-petroleum jelly. Lubrication removes residual oxide film and prevents it from forming again.
Before crimping, copper wires are also treated with a grease containing only technical petroleum jelly, without quartz impurities. This lubrication reduces friction and reduces the risk of core damage.
Fears that a non-conductive grease will increase the transient resistance of the joint are not viable, since when the technology is followed, the grease is completely displaced from the contact point, remaining only in voids. The surface of both sleeves and conductors must be lubricated.
The ends of the veins of cables of figured cross-section, for example, triangular, before installation in the sleeve must be compressed to a round shape using a separate figured press.
Before connecting by crimping, the wires are inserted into the sleeve until they stop. The joint should be located exactly in the middle of the sleeve. Then, alternating crimping is done on both sides of the sleeve. Two indentations are made to connect the aluminum wires per side, and one indentation is sufficient for copper wires.
Perhaps the connection of the wires is not end-to-end, but with the plant on one side. In this case, the total cross section of the wires should not exceed the cross section of the sleeve itself.
In the case of local indentation, the quality of the contact joint is normalized by the depth of the pits, measured with a special probe or vernier caliper. When using continuous compression, the overall dimensions of the resulting multifaceted section are controlled. Norms of all these sizes are given in special tables.
After crimping, an external insulating layer is created at the junction. To this end, you can use varnish and electrical tape. Before installing the sleeve, you can put it on one of the connected cores shrink tube, which subsequently closes the connection completely securely. After installation, the tube can be heated using a conventional gas burner.
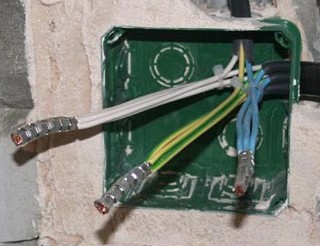
Common errors when connecting wires by crimping
Very often, a sleeve of an inappropriate cross section is purchased for connecting by crimping. If it is too small, then for installing the core in the sleeve, part of the conductor is cut off. This is unacceptable, because it not only reduces the cross section of the wire and increases the transition resistance, but also creates a mechanically weak spot on the wire, in which it is likely to subsequently break off. This is especially true for solid wires.
Too large a sleeve also does not benefit the connection: crimping and contact will not be particularly reliable. Stranded wires, if absolutely necessary, can be folded in half, but this will not solve the problem of mechanical strength of the connection.
In no case can you cut the factory sleeve, make it shorter, no matter how you want to make the connection point less extended - all this can lead to an increase in transition resistance and a decrease in the reliability of the connection.
Very often for crimping sleeves and tips used ... ordinary hammer. But I must say that it is very difficult to get a reliable connection, and it is even more difficult to control its quality. Therefore, it is better not to save and purchase a special tool for crimping.
See also at bgv.electricianexp.com
: