Categories: How does it work
Number of views: 13158
Comments on the article: 1
How do cables and wires
The process of manufacturing wires and cables is technologically implemented in several steps, the main of which are: drawing the workpiece, applying insulation, and the final stage is winding the finished product into bays. In fact, everything is somewhat more complicated, and at least two large workshops are allocated for cable production - a workshop for processing copper billets and a workshop for applying sheaths.
In the first workshop, the copper wire rod is drawn into wires and twisted, and already in the second workshop, the workpieces are passed through extrusion lines, where the cable takes on a completed insulated shape and is wound into coils.
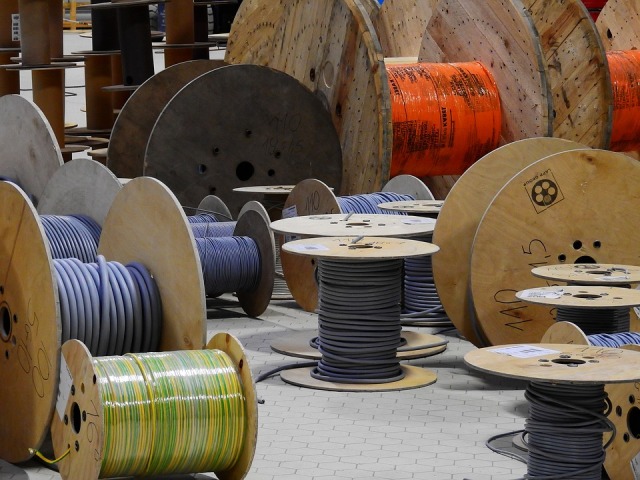
Let's, however, consider the technological process for the production of cables and wires in more detail and step by step on the example of the production of PVS brand wires.
The raw material for copper conductors is the so-called wire rod, which is a relatively thick copper billet with a diameter of about 10 mm, and they are delivered to the plant. Here, using a coarse drawing machine, the copper wire rod is cold worked - it passes under pressure through a drawing tool, the so-called die, whose channel is much smaller in diameter than the wire rod itself.
Thus, a thin long wire is obtained, the diameter of which is many times smaller than the diameter of the wire rod, and the length, respectively, is greater. The drawing machine yields pasma - thin wires, which then turn into a multi-wire structure - a rod.
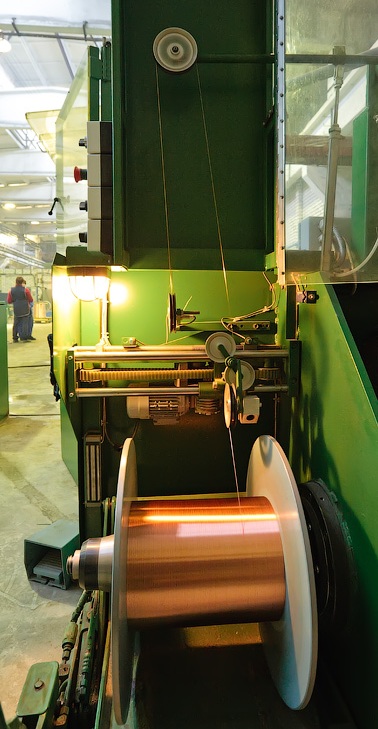
In the process of wire drawing, the conductive and plastic properties of copper deteriorate, therefore, in order to return the conductor to its proper properties, the resulting wire must first be heated in a vacuum oven to a certain temperature, and then cooled to room temperature to make it softer.
This procedure is called annealing, and the duration of exposure of the skein in a vacuum furnace and the heating temperature depend on the initial and required characteristics of the wire, as well as on its diameter. After completing the annealing, the strand with the correct electrical and mechanical characteristics is wound on coils for feeding to the next processing step - for twisting into a strand.
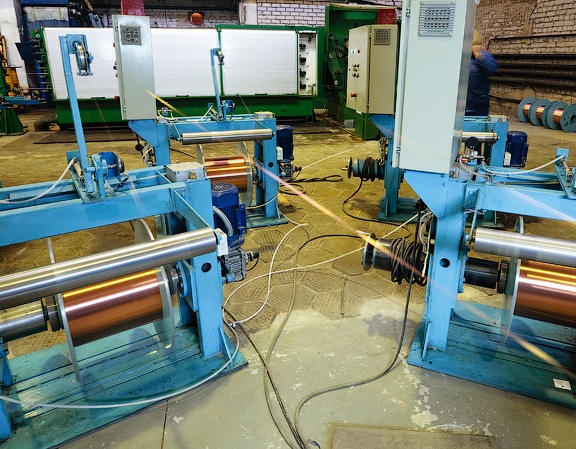
To create a flexible multi-wire core of the future wire, individual wires (thread) from several coils are simultaneously fed into a twisting machine, where a conductive core, a strand, is twisted from them, which serves as the basis for the future wire. Twisting can be different: sheaf, cord, right, and also can have one or another direction (right or left).
Depending on the required flexibility, tensile strength, and other characteristics of the future wire, choose the type of twist. United by twisting into a strand, the wires are again wound on a reel. As you already understood, a strand is a multi-wire wire, ready for insulation.
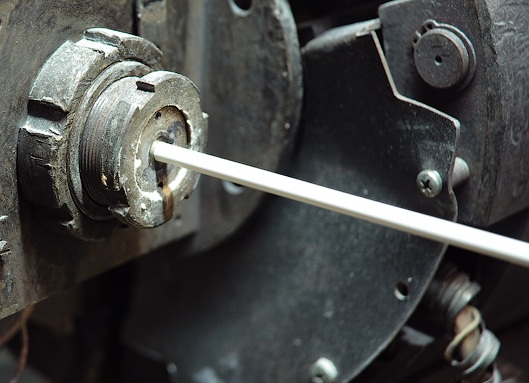
The strand is fed into the extrusion complex. Here, the granules of PVC compound and turn into insulation. The coil with a strand is mounted on a delivery device, from which the twisted core is fed into the extruder. The core is constantly tensioned with a special tensioner, and is immediately heated to 100–150 ° С by electric current, while it passes through the rollers. Granules of PVC compound molten in the screw turn into a homogeneous mass. The heated wire passes through the extruder, where the molten mass of PVC compound is extruded onto it, acquiring the shape of a sheath.
The operation of the extrusion line in the technological process in the manufacture of cable:
After exiting the extruder already in isolation, the flexible wire passes through an extended cooling bath with water, in which it is cooled to 60 ° C.Then the water is blown off the wire with a special device, the insulation is finally dried, and the insulated wire is fed to the shaft, before being subjected to a dry insulation test.
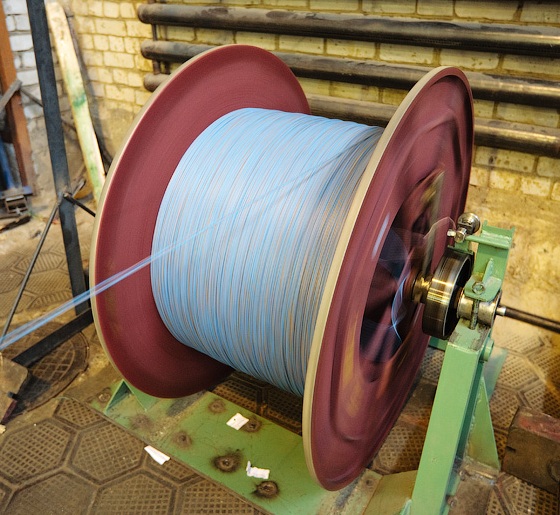
Separate insulated conductors are finally twisted - this is how they get a stranded wire: twisted conductors are fed into a twisting disk machine, and they are compacted. At the final stage of production, twisted cores are coated in the extrusion line with general insulation, and the finished wire is tested for compliance with GOST. After that, the wire is packed in bays, and the bays are then shipped.
See also at bgv.electricianexp.com
: